由于对能效和耐久性的要求的不断提高,铸造工艺为制造出新一代轻质结构汽车提供了多种可能性,其所面临的挑战不仅仅是新材料的更替,还需要找到工艺环节中的统一有效解决方案。
部件研发
J.-M Segaud 从宝马集团的角度出发始终在探索着一个问题,那就是在迈向电动汽车时代的今天,铸造在未来是否还可占有一席之地。答案显然是肯定的。关键所在是采用具有少材料应用、低能耗、方案和部件数量可灵活改变的优点的轻质结构和制造工艺,并可通过最少的投资来实现。整个制造工业可能将面临一次深刻的转变。全面应用的数控产品和生产方式,联合外包以及3D打印技术都提供了多种可能性,未来所有产品均可实现定制化,高灵活性以及低成本制造。不仅仅是电动汽车改变了铸造业的未来,不断增加的效能和耐久性要求也发挥着不可忽视的作用。作为关键的一个环节,铸造业有可能为实现新一代汽车的轻质化生产画上浓墨重彩的一笔(图1)。其所面临的挑战不仅仅是新材料的更替,还需要找到工艺环节中的统一有效解决方案。
C. Wilhelm看到了铸造工业所面临的挑战,虽然具有很高的投资潜力。但采用铸造和变型制造工艺制造轻质结构的辩论也日益激烈,金属和非金属材料应用的争论也到了白热化的阶段,节能和减重要求也成了必须要面对的实际问题。因此铸造公司必须寻找新的机遇,从而在层出不穷的新工艺和新材料时代保持竞争力。电动汽车就是一个很好的示例,在新的应用领域中传统铸件已经再无用武之地。
另一个例子是S.Heinrich所述的战略,模具生产商采用适合的设计,用轻金属结构部件替换重钢板。所有大型汽车生产商均在推动使用轻金属结构件替换重钢板。这对于压铸行业来说不仅仅是挑战,也是机遇。对于总部位于来明恩的Schaufler模具有限公司来说,在压铸模具研发和生产方面必须考虑到上述问题。
P. Reichen 从压铸机生产商的角度着眼于轻金属压铸行业的未来。未来压铸件在保证结构和功能的前提下会越来越薄,越来越轻,制造工艺也越来越复杂,同时还要满足节约资源和降低成本的要求。而且在汽车制造中对铸件也提出了更多要求。当代和未来的压铸件面临的挑战是:使用铝材和镁材制成的大型复杂结构件替换昂贵的多部件组合构件,同时对压铸件工业也提出了新的要求。可实时调节的压铸机可制造符合要求的高品质部件。其基本的前提条件是,使用最少的材料和能源制成任意形状,集其他功能于一身并可进行持续开发的压铸件。通过现代化的压力铸造技术提高生产率和质量是保持压铸件长期竞争力的关键要素。(图2)
在进一步节油的背景下,在考虑降成本和保护环境方面,J. Goroncy [5] 看到小型个人汽车使用3缸和4缸汽车发动机的发展趋势,目前该发动机比纯电动发动机更具竞争优势。该发动机的优点和能效已经在奥迪、大众和丰田汽车上得到了充分的展现。
铸造设计
R. Gorski 介绍了新式连铸欧洲标准16482。该新标准中对客户和生产商的铸铁连铸特点和特性进行了充分介绍。在设计、生产和质量控制方面双方已设定了明确的前提。可从柏林Beuth出版社获得完整的DIN EN 16824:2014 标准,并经过德国标准化协会(DIN)的批准之后方可发表。
H. Werner和I. Lappat 举例介绍了风能发电机机架铸件,设计部和铸造车间应多沟通并交流意见,在研发阶段尽早排除问题并制定对双方来说均可靠的制造方案。从而制造出更高功率等级、更节能并符合低功率等级尺寸和重量的机架。
为了达到类似的节能效果,其他风力发电机生产商应首先进行试验,使用混晶固化的球墨铸铁制造出其他铸件(转子轮毂和机架),并通过减少壁厚实现减重的目的。使用符合表格1中要求的材料Ferrocast。
部件和组件的标准化计算可为设计师提供支持,并加速整个研发流程。#p#分页标题#e#
位于考布伦茨的能动和非能动安全系统TRW的主要供应商,也是制动技术的欧洲技术中心,可使用Ansys工作台[8]进行自动化模拟。模拟过程自动化项目的目的是减少不断重复的工作的消耗、提高效率、降低成本、缩短项目处理时间并通过模拟应用对项目开发进行全面支持。专业人员的模拟任务转交给了设计师。但是前提是实现流程的标准化。
A.Rennet介绍了未来车身制造中的材料开发和状态。当今汽车产品结构的轻质化,使用多种可回收材料和多用途材料解决方案已经在行业内铺开。开发者可使用多种不同类型的材料实现最佳材料组合,无法预计成本构成。在材料确认之后才可确认部件成本,但是此种复合材料的成本无法预计。通过详细成本分析核算,除了要考虑不同材料和结构设计的制造成本和材料成本之外,还可通过选择框架参数实现其他轻质结构从而制定出适合的材料方案。
模拟技术
C.Thomser, M. Bodenburg 和 J. C. Sturm 介绍了一种使用周期性材料参数进行铸造过程模拟Magmasoft的方法。在BMBF-研究项目框架内,MABIFF首次在铸造中使用不同的材料。显示组织结构情况的Wähler曲线填补了铸造过程模拟和载荷分析之间的空缺。通过运行强度计算得到制造流程中的特性。此种创新性方法不仅能够在数级和量级上延长使用寿,还能增加载荷循环数,并准确的预知出裂纹的位置,相对于传统的铸件设计来说,已经取得了非常大的进步。
G. Friederici介绍了位于邵平根的AXA设备开发和制造有限公司,这是一家专注于加工中心以及定制生产设备的研发、设计和制造的公司,在模拟领域中使用CADFEM提供的软件ANSYS可生产出更高刚性和具有材料优化特点的部件。
铸造材料
铸造材料的使用范围越来越广并不断扩大。开发出的高性能材料为设计者提供了更佳并适用于不同应用条件的选择性。下面介绍几种最重要的铸造材料的最新研发情况和技术水平,如镁,铝,铜,铁,钢和特殊材料及在2014年专业杂志中发布的复合材料。
镁材
L Kallien, T.Weidler和M.Becker 描述了镁铸件热室压铸工艺的气体辅助注射技术研发和应用情况。目的是为汽车车身结构开发出一种由轻质镁材料制成的结构件(图3)。相对于钢或铝来说,镁金属的弹性模量低,并可通过气体辅助注射技术制成的通道对部件结构硬度进行补偿。
铝材
2014年国际铝铸造竞赛的获奖者,获得纽伦堡举办的2014年欧洲铸造大奖。位于杜塞尔多夫的铝工业委员会(GDA)举办了第六届国际铝铸造大赛。德国铸造工业(BDG)联邦协会也赞助了此次大赛。多年以来铝压铸件大赛已经成为了一个展示最高品质铝铸件的专业平台。大赛的评估标准是:新颖、创新和技术进步。获奖产品见图4。
S. Wiesner 和 L. Speckert 介绍了Georg Fischer汽车制造商在AluSiDur结构件上使用的一种新式高硬度铝压铸合金材料。对合金材料AlSi10MnMg的成分进行调整之后,静态和动态强度值明显增加,经过T6-热处理之后变形量更小,屈服强度达200N/mm2,壁厚1.9mm的结构件的断裂延伸率达8%。
B.Fuchs 等人描述了在AlSi 10MnMg合金结构部件中注入盐芯并经过热处理的试验情况,不需要在前一个加工步骤中去掉包封的型芯。在特殊情况下,可通过固溶退火步骤进行热处理,并在水池中淬火,然后在未加热的隔离环境中检查热时效情况。盐芯中保存的余热可持续释放进行热时效。同时确定模拟试验中固溶化淬火和隔离热时效的传热系数。
E. Sterling 中描述了一种具有可调性能的铝合金的制造流程和实际应用情况。可调性能的铝合金开创了一种新的可能性,合金溶液的最重要的特性与原子结构和稳定性有着密不可分的关系。通过AMS-方案(合金记忆结构)促进具有现象记忆功能的二相MSM-流体系统的开发。同时也是熔液特性和产品特性之间的中间环节。
D.Dragulin和M. Delbrück 分析了在规定热处理条件下极薄壁铝部件的压铸技术可能性,从而获得绝佳的强度和延展性。其分析结果与对汽车薄壁铝压铸件进行热处理后的情况一致。#p#分页标题#e#
W. Nawratil 介绍了设计师目前可使用Gleich铝材有限公司新开发的特殊铝材G.AL-Dynamic替代具有相同动态载荷强度的轧制部件和钢材的情况。一方面新材料具有更高的抗疲劳强度以及明显改善的断裂延伸率,不仅具有良好的减震特性,同时使部件寿命增加了40个系数;另一方面具有良好的可加工性、形状稳定性并且生产成本更低。
锌材
在中介绍了2014年在纽伦堡举办的第五届欧洲铸造大赛中的获奖锌材压铸件。铸件质量虽然无法达到“设计/铸造技术”,“转换为锌压铸件”和“表面技术”的要求。因此根据所有评估结果同时选出了在锌压铸方法中具备优秀的锌材加工性能的三个获胜铸件(图5)。
铸铁
C. J. Heckmann 和 W. Stets 研究了球墨铸铁中非金属析出的原因、影响和预防措施。熔液中的氧含量在经过镁元素处理之后以及铸件中剩余镁含量对非金属析出有非常明显的影响。在操作过程中可以确定,由于存在非金属残留物会降低材料的疲劳强度。同时还显示,非金属材料析出还可造成内部组织非同质性,例如出现缩孔。
B.Schelnberger, B. Pustal和A. Bührig-Polaczek 对球墨铸铁中的非金属杂质含量进行了分析和模拟,非金属杂质会影响交变抗弯曲强度和断裂延伸率。因为非金属材料一般集中在晶界附近。通过热动力方法检查含多种黑色镁材料杂质的生成原因,可通过补充实验和创新特性分析方法描绘并评估上千个颗粒的形状、尺寸和成分。通过球墨铸铁的热动力模拟方法可显示出镁的偏析特性。
S. Borgs和W. Stets 介绍了AiF要求的研发项目,显示多孔性增加对GJS样件机械特性的负面影响。观察多孔性等级1中断裂延伸率验收时的特性参数变化,抗拉强度和屈服强度与标准样件相比并未出现变化。达到多孔性等级2和3时强度受到很大影响,并且断裂延伸率明显下降。在多孔性等级1时,与标准样件相比抗疲劳强度下降了约8至10%。在多孔性等级2或3时,与多孔性等级1相比样件的抗疲劳强度有明显下降(相对于标准样件来说也明显下降)
P. Mikoleizik和 G. Geier 介绍了海上风能铸造材料开发文件第1部分中的兆瓦级别范围内对海上风能发电机组中铸铁材料SiWind(GJSF-SiNi30-5)的高要求。从2006年到2012年,很多公司和机构共同开发了MEGAWind项目,同时也是联邦环保局、自然保护局及建筑和核反应堆安全局(BMU)的研发项目,该项目致力于开发出适用于海上风能发电机组的高强度和高延展性的结构部件所使用的材料。在表格2中列举了EN-GJS-400-18-LT不包括的其他新材料的静态参数。
C.Bleicher等人 在位于达姆施塔特负责检查运行强度和系统高可靠性LBF的弗劳恩霍夫研究所进行了第2部分检查,计算了周期载荷下大壁厚材料的载荷能力。在全面的试验流程中确定新材料的抗疲劳强度。通过力和延伸率检查确定材料SiWind的周期材料特性以及平均应力和缺口强度。在力度调节弯曲试验中确定各种厚度铸件的组织周期特性和铸铁层影响(表格3)。
J. Egge和J. Meyer 对新式混晶硬化铸铁材料SiWind的材料断裂特性进行了评估。进行了断裂力学分析,例如转子轮毂。转子轮毂材料符合风力发电设备材料的高强度要求,可增加硅含量来提高强度。
C.Bleicher等人介绍了位于达姆施塔特的负责检查运行强度和系统高可靠性LBF的弗劳恩霍夫研究所的检查结果,其中对三种铸铁材料EN- GJS-400-18U-LT, EN-GJS-450-18 和 EJM- GJS-700-2进行了低温使用情况检查,例如在室温和e=-40℃时的周期性常规强度试验。两种铁素体类型的抗疲劳强度从4%提高到了7%,珠光体材料EN-GJS-700-2在室温下过渡到-40℃的过程中,循环强度下降了6%(表格4)
M. Antes 提示,高硅含量球墨铸铁可与液压钢媲美。很多设计者认为,可延展铸铁类型无法经受高压因此无法取代钢材。但是新式的高硅含量铸铁类型打破了传统观念,它可以经受高达900bar的压力(图6)。#p#分页标题#e#
R. Gorski介绍了在弗莱堡矿业学院计算新EN1648:2014 GJS中连续铸造合金的结构力学特性。材料试验显示,球墨铸铁在连续铸造中具有非常好的材料特性。在试验温度中扩展裂纹不是硬脆性而是可延展性的。组织结构对材料特性的影响为铁素体减少,珠光体增加。每个部件都均进行断裂力学检查,只能在限定条件下保证连铸的工艺特性,因为圆形和方形的铸造半成品必须保持稳定的铸造条件才能获得一致特性。因此,例如裂纹开端和裂纹扩展均与组织结构,粒子大小以及铸造参数有关。在连铸时要保持铸造参数不变,才能保证获得符合标准的材料参数或指定的最小特性。
M. Lampic和M.Walz在由多部分构成的综合性出版物中介绍了含蠕虫状石墨(EN-GJV)的铸铁材料。在第1部分中对材料进行了定义并简要介绍了GJV的情况。在40年后的今天,蠕虫状石墨的铸铁材料(GJV,CGI)早就广为使用,也不再扮演配角,而成为了必要的“适合”结构材料。在报告第2部分中介绍了GJV 的组织结构,含Fe,C,Si,S,O,Mn,Cu和Mg的蠕虫状石墨晶体结构。第3部分中介绍了GJV的技术特性(抗拉强度,屈服强度,弹性模量,减震特性,压力载荷特性,硬度,耐磨强度,疲劳强度和韧性以及物理特性(导热性,热延伸系数和特殊热量))。本出版物第4部分中介绍了能源和破坏之间的关系,解释了铸件,寿命周期和断裂力学中形成能量连接颗粒的“破坏原因”,。在第5部分中作者介绍了GJV 铸件必要的后续处理工作,包括热处理、生产焊接和切削等必要加工操作。
E.Fritze和A. Rimmer在[34]中介绍蠕虫状石墨(EN- GJV, CGI-450 参照ISO 16112)铸铁材料,在高载荷NKW发动机中使用发动机缸体铸件。在上述出版物中已经进行了详细介绍。
钢材
铸钢公司Sande从2011年开始从事30吨以下GX13CrMoCoVNbNB9-2-1的铸造生产,是利用高合金材料制造动力技术铸件的领先公司。从2011年开始生产了800多吨(发货重量)由CB2-材料制成的应用于发电站中的钢铸件。高要求的铸件包括厚壁缸体,进入管,肘管,高压和高性能蒸汽涡轮机的中压内壳体。
位于拉德福尔姆瓦尔德的Klaus Kuhn不锈钢铸造有限公司开发了定制尺寸卷筒材料,1.2396号材料(G22CrMoVNb6-12)和1.4317号材料 (GX4CrNi13-4)。铝板、铝带和铝膜的需求在过去几年中持续攀升。对生产商生产铝卷的载荷和持久性要求也逐渐提高,因此对卷筒使用的材料的要求也逐渐提高。铸造公司现在可使用高强度和高品质的材料,用 1.2396 号材料(G22CrMoVNb6-12)生产卷筒,此种材料完全可与常年以来经证明有效的材料解决方案相媲美(RP0.2 至少为850MPa),完全符合滚筒的最低强度要求(Rm=1100MPa和至少10%断裂延伸率)。
在中报道了萨尔茨基特股份公司,SMS西马克和克劳斯塔尔工业大学已经成功将钢材水平带铸法运用到工业生产中。相对于已知的钢连铸法来说,该工艺生产的钢带薄了20倍,而且不需要热处理、轧制以及冷却加工流程。
D.Li和C. Sloss 介绍了一种铁素体不锈钢(FSS),此种材料的某些特性适用于汽车工业中的尾气排放部件,具有很好的抗氧化性、极低的热膨胀系数并且造价低廉,而且不需要添加镍金属。此种材料还适用于制造排气弯管铸件和涡轮增压压缩机铸件。报告中还包括合金开发的现骨干介绍。介绍中的材料评估包含了化学分析,微观结构,抗拉强度,硬度,热氧化性以及铸造状态下和热处理之后的样件热应力疲劳特性并检查了尾气弯管的耐热性。螺旋铸造试验中显示,FSS与耐热奥氏体与不锈钢相比具有较低的流动性。
D.Kuhn 介绍了轻质结构。为了制造出更轻的车身,催生了采用纸-钢板-复合材料制造车身板的想法。材料专家不仅仅局限于传统材料的使用,如钢材、新兴材料如铝材或甚至镁材等,还将目光转向了轻质的非金属材料。现在造纸生产商也成为了轻质车身的材料供应商。例如慕尼黑的造纸工艺基金会主导了一个开发制造薄壁高强度车身板的纸-钢板-复合材料项目。
铜材料
在中介绍了每年约有250000人访问最重要的有关铜材料的德语网站,德国铜协会网站发布了所有与铜材料有关的问题。为了更好地满足使用者的要求,现在网站重新进行了改版,从而可以更好的针对各种技术问题进行有针对性的解答,并详细介绍新的内容设计。#p#分页标题#e#
部件的几何结构越复杂,使用金属粉末进行喷射铸造(MIM)的方法就越经济适用,并可使用消失模法制造。总部位于乌尔姆的维兰德工厂股份公司利用两种方法制造了铜材料的高要求部件,并且无需进行后续加工,在中进行了详细介绍。消失模金属铸造和金属粉末喷射铸造(英语:Metal Injection Moulding,简称MIM)是非常适用于制造形状复杂部件的制造方法。两种制造流程可以很好的相互补充,适用MIM方法可以制造大数量甚至百万件从1至100g的轻质部件。同时消失模方法也适用于制造少量重量大的部件。
特殊材料
O. Köser 等人通过虚拟过程建模的方式对Ti-6AI-4V-结构部件的离心铸造过程进行了检查。汽车和航空飞船中通常使用大型钛金属结构部件,不仅可以减轻重量,还可减少燃油消耗和有害物质排放。从节省成本的角度出发,还可使用离心铸造方法制造结构复杂的部件。主要优点表现在铸造建模的性能特点上(材料特性,模具和熔液的传热系数,边缘条件),如建模结果与真实的铸造结果一致,并可采取稳定和改进铸件质量的措施。
轻质结构
金属塑料复合材料的研发目前是开发最新车身结构轻质结构的最新科研领域。宝马集团的工程师通过多功能材料复合技术成功将不同的材料整合在一起并获得了了良好的效果。宝马已经在整车部件中采用了不同材料的复合工艺。车身中使用大部分轻质结构不仅能够降低重量,还能更好的改进功能。不仅可以增加车身刚性,还可提高减震舒适性和控制精确性,同时车身重量减少还有助于提高效率和汽车灵活性,并有利于提高车身动力。
现代化的混合和复合材料应用对航空业也非常重要,低重量和高稳定性的材料已经成为了行业首选。此种材料不仅能够满足减重的需要,还能满足高强度和刚性的要求。工业和手工业材料处理委员会(IKV),RWTH 亚琛,在其他应用中也首推此种材料。目前通过焊接或螺栓连接的金属部件可通过喷射铸造方法的适合塑料支撑的固定装置形成材料连接。
部件特性
P. Kainzinger和F. Grün 检查了在不同的冷却和凝固条件下球墨铸铁部件的局部不同质组织结构(EN-GJS)。由于显微结构对材料强度有着非常大的影响,因此局部强度数值可能会不同。在特殊情况下,如果局部组织结构的差别达30%,则抗疲劳强度会受到很大的影响。此外还介绍了两种材料模型(图7中的实际模型,图8中的断裂力学模型),通过该两种模型的铸造流程模拟测量局部材料周期特性。对不同尺寸的样件进行试验显示,随着样件尺寸的增加,抗疲劳强度也明显下降。最后根据局部材料系数在优化循环中对展示的材料模块进行总结。可在制造条件的作用下对部件进行优化,从而充分发掘出材料的轻质化潜力。
P. Langenberg 在两部分构成的出版物中从焊接技术的角度通过断裂力学计算方法分析了整个寿命周期。通过断裂力学计算方法分析金属部件中裂纹或类似缺陷的影响。出版物第1部分中介绍了导致出现裂纹的力量情况。第2部分中介绍了抗裂性计算方法和不重要的裂纹增长计算方法。
在介绍了辉门公司在维斯巴登技术中心开发了新式无铅轴承材料,该材料通过聚合物涂层IROX获得更高的抗机械载荷能力。复合材料可针对相应的载荷位置选择适合涂层的轴承套。轴承涂层可报考阴极真空涂层,多聚物涂层或电镀层,涂层可提高发动机的稳定性。使用无铅合金可增强抗疲劳强度。使用高强度无涂层铝合金的趋势已经到头了,可根据需要增加IROX涂层提高负载能力和耐磨性。
铸造应用
制造技术和材料应用研发的弗劳恩霍夫协会与位于不莱梅的Lloyd Dyna¬mowerke有限公司联合开发应用于铸造发动机的使用消失模方法制成的铝材料(图9)。制造轨道驱动的铝线圈,然后进行安装并进行测试,目前来看测试结果很成功。从技术角度上来说比原来使用的铜线圈性能更好。容积效率和冷却效率可通过铸造技术中的自由造型明显提高。铝线圈的使用可以明显减少原材料成本,重量以及损耗。#p#分页标题#e#
在中展示了使用铝合金A356-T6支撑的移动式电气设备重量经过优化的把手,如极轻结构的加强筋和精密铸造方法中的精确配合件,虽与浇铸部件相同,但是无需进行后续加工 ( 图10 ) 。
J. Goroncy 介绍了KSPG股份公司在哈尔茨格罗德和内卡尔苏尔姆以及在中国的铝结构部件压铸制造中成功开发了铝结构件,包括纵梁、支柱和减震器支架的制造。
在 中报告了2014年欧洲铸造的情况,报告中展示了第六届国际压铸竞赛和第五届锌压铸获奖作品的图片并进行了文字介绍。
目前为止只能使用精密铸造法制造少量复杂部件,耗费时间长并且费用高。位于埃内佩塔尔Schmolz + Bi¬ckenbach铸造有限公司经过试验之后发现情况大有改观。位于埃内佩塔尔voxeljet技术有限公司,弗里德贝格使用3D打印技术制造了消失模。3D打印技术的优点除了具备经济效果之外还能减少制造时间并提高订单数量,2013年的精密铸造公司投资了一台的voxeljet打印机。现在可打印的PMMA-材料制成的部件结构尺寸可达到1060 x 600 x 500 mm,可制造的部件最大单位重量为70公斤(图11)。
U. Hewelt和A. Skarjalis 介绍了措勒恩在索斯特工厂的铝精密铸件规格。除了能够快速制造样件和小批量部件以及仿生结构部件之外,还能按照Sophia方法制造具有特别高机械特性的铸件,铸件可根据计算的优化调节凝固超过标准数值,并可用于制造其他轻质结构。根据该方法制造的赛车摩托车(图12)的后轮震动平衡杆获得了2012年的欧洲铝材料大奖。
在中报道了瑞士沙夫豪森GF汽车在2014年连续第二年获得了“铸件设计”范围内的国际镁材料(IMA)的设计大奖。获奖者是来自奥地利的GF汽车铸造公司,Altenmarkt为保时捷Panamera制造的镁材料合金油管模型铸件(图 13)
在中介绍了第9届中国国际压铸大会中展示的两款优秀奥迪A6(图14)的悬挂托架铸件,一款是来自中国苏州Georg Fischer汽车部件制造的轻质部件,另一款来自浙江VNV金属产品有限公司制造的高速列车(图15)的轴承套,两种部件满足所有优化工艺参数,且无缩孔并且具有高承载能力。
位于帕彭海姆的家族企业Krause-精密硬模铸造有限公司为国际市场提供特殊制造的铸件,可满足不同设备的多种需求,重要部件例如控制杆,变速叉,手柄,夹钳,衬套和泵工作轮,以及护壳和盖板可通过硬模制作方法制造。铸件可使用不同的铜合金和铝合金制造。根据计划的应用范围和要求硬模铸件可使用不同的材料制造。
作为德国高品质铝管接头的供应商,Brinck铝铸造公司可制造硬模铸件中的复杂轻质模制件。(图16)产品组合中包含上百个不同的管接头,大部分管接头均为特殊形状。生产的管接头广泛应用在连接技术,机械和设备制造,汽车制造或舞台技术的栏杆中。当然管接头的批量生产只是Brinck的一个领域。多年以来该铸造公司一直作为很多行业的设备部件传统供应商,例如机壳部件,风扇叶轮,把手,安装轨道和设计部件。产品范围从设计延伸到工具和模具制造再到铸造的整个工艺环节,包括机械加工和表面改善。在大多数情况下在哈恩铸造厂完成预制部件和组件。
#p#分页标题#e#
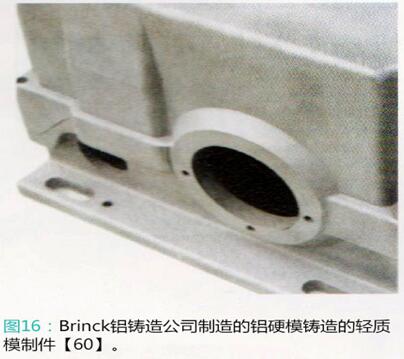
Y. Fasoyinu, D. Weiss 和 J. Shah 介绍了一种由砂型铸造法转换成硬模铸造法利用高强度铝合金 A206 制成的高载荷制动件(图17),可根据精密型芯成型实现更好的使用特性。
“Hyundai Together”集装箱船上使用的世界级113吨重量和10.3米长的集装箱窗螺栓在梅克伦堡州的金属铸造有限公司(MMG)制成。
位于奥尔斯贝格的Olsberg Hermann Everken有限公司是室内空气隔离壁炉的世界领先生产商。除了壁炉和木质颗粒炉之外,还可制造铸铁和薄铁皮制造的工业产品,拥有与室内空气隔离的各类壁炉。该公司多年以来一直是欧洲市场的最大供应商。奥尔斯贝格在2004年制造出了第一个与室内空气隔离的壁炉“Mayon”,并且是该领域的先驱者。除了非常成熟的燃烧工艺之外,还以申请专利的涡流燃烧室著名,还包括已经申请专利的闭门系统,该系统可持续密封燃烧室并封锁噪音,以及家族企业以设计为主的产品。
在中介绍了从防火角度出发在隧道施工中可延展铸管的应用。多年以来一直使用可延展铸铁制造的灭火水管。材料选择委托人的重要判断依据是管材料的高安全性以及高内压载荷时的纵向力连接技术的载荷能力和可能的压力冲击。该应用范围内超过400000米铺设的可延展铸管。另外对Duktus管道系统有限公司,韦茨拉尔在苏黎世的跨城市管道项目,在梅拉诺镇的西北方向并通往耶拿亚格德山隧道。
在报道,Heger铸造有限公司在恩肯巴-阿尔森博尔恩制造了13000公斤重的风力发电机轮毂,是目前该公司有史以来制造的最大铸件。
位于克雷菲尔德的Siempelkamp铸造有限公司在2013年连续创造了三项世界纪录,如[66]中报道的那样。在2013年7月12日制造了296吨铸件。一周之后使用301吨钢水制成了世界最大的铸件,并通过铸造压力机铸造成下纵梁,目前已经折断。使用320吨钢水分配在五个钢包中,Siempelkamp在2013年9月11日超越了他上一次世界纪录并铸造了一个完整的独一无二尺寸的铸件。
在中报道称,位于克雷菲尔德的Siempelkamp-铸造公司拥有260年大型碾磨机齿轮制造的经验。公司在新成立的制造车间可生产达22米的齿冠。可通过独立铸造技术制造出碾磨机械中应用的越来越大的铸造部件。
C.Gärtner 介绍了一种由位于美国中部萨斯菲尔德的辉门公司使用新开发的活塞环铸造工艺制造出更高活塞环质量的新式铸造技术。铸铁材料GOE70制造的高品质活塞环采用一种自动的垂直成型方法制造,该方法可以更好的保证制造技术。通过对卡车柴油发动机的检查发现,活塞环齿面的磨损非常小。
在中介绍了现在可使用激光方法制造大型抗机械载荷和热载荷部件的方法。使用粉末层为主的激光熔炼方法可制造复合材料540mm高的结构空间(图18)。目前在汽车
工业中主要使用铝合金,在早期开发阶段中替换高成本砂型铸造和合金铸造方法。此外目前使用钛材料和以镍合金为主的要求越来越高。首先材料等级适用于航空航天中的极端要求。除了驱动技术部件之外,还包括航天领域的测试载具,发电厂技术或飞机制造中的涡轮机部件。激光加工方法还可用于涡轮机维修。
在中介绍了“现代铸造”杂志中刊登的年度最佳铸件。2014年铸造公司Aarrowcast,沙瓦诺县,美国,WIS获得了使用砂型铸造方法制成的GJS机油盘大奖(图19),经过 FEM分析,除了重量降低了,其性能也得到了优化。这里也简要介绍了其他奖项,它们因材料节省,性能完善和复杂的铸造成型工艺而脱颖而出:在中,作为最好的镁铸件介绍了一种用镁铸造而成的电子载体;作为最好的铁铸件介绍了一种由 GJS 铸造而成的叶轮;作为最好的钢铸件介绍了一种由 W.- 4140 号钢铸件制成的精细成型刀架;作为最好的铝铸件介绍了一种用铝低压铸造而成的水分配管,以及由 GJS 砂铸而成的副车架铸件和铝铸鼓风机外壳,皆因将多个零件整合成一个铸件得到的复杂铸型而出众。#p#分页标题#e#
Z. Linxi 等 介绍了运用各种生成技术以钛合金、钴铬合金和CoNi合金等特种合金铸造生产用作医用植入物的多细孔零件。