对于压铸生产工艺来说,压铸模具决定了产品性能,经济性,产品质量以及生产率。
材料篇
铝合金
S. Wiesner 和 L. Speckert向我们介绍了结构件应用中所需的高强度铝制压铸合金AluSiDur。此合金材料是在AlSi10MnMg的基础上加工而成的,并相应的在化学组成和热处理方面做了改进。因此它可以通过T6处理和水淬处理, 在断裂伸长率约9%的情况下, 屈服强度Rp0,2达到280MPa。通过进一步的改进, 还可以在无需进行任何热处理的情况下达到约200MPa的屈服强度。(图1)
用于结构件的铝制压铸合金中铁和铜的含量都较低。R. Donahue 特别研究了铜含量对结构件的影响。根据研究结果,合金中较高的铜含量,能将铁的比例提高到0.4%(所有数据以百分比计)。这样不仅可以通过提高铜含量改善流动性,而且在进行T5热处理之后,屈服强度可以明显提高50%, 进行T6热处理之后甚至提高100%,从而使制件重量大幅度降低成为可能。
S. Midson 和 J. Brenan对在进行T5热处理后, 合金360和A360(类似 AlSi10Mg)中铁含量对于机械性能的影响进行了研究。在受NADCA委托所进行的这项研究中,铁和镁的含量, 以及热处理参数温度和时间发生了系统性变化。
E. Ambos等人描述了,在尽可能保证轻质结构的前提下,铝压铸件的目前状况和未来前景。对高应力发动机架孔隙率的研究有助于建立合金GD-AISi9Cu3(Fe), GD-AI-Si10MnMg(Panfoundal)和GD-AI-Si8MnMgSr (Silfoundal)的孔隙率与可达到的强度性能之间的关联。对不同热处理样品进行疲劳试验的结果表明,迄今为止所使用的铝合金的强度潜力是相当大的。在允许公差范围内对合金组成成份进行优化,以及降低孔隙率可以增加这一潜力。
R. Klos 和 P. Kohlmann 以合金Castasil-21 (AISi9Sr)为例,描述了冶金铝压铸合金所能达到较高的传导性。合金中所加入的锶使共晶点降低约6至8K,从而产生共晶硅的珊瑚状结构,并使断裂伸长率提高至约5%。此外,合金对于压铸模具钢料的亲和性降低,这将对合金0.5%至0.7%的铁含量带来有利的影响。在表1中对不同铝制压铸合金的技术特性进行了比较。
W. Fragner等人研究了再循环合金在汽车制造行业结构应用领域使用的可能性。所研究的各种合金,机械性能通过金属模铸件样本来进行测定。
用AISi10MnMg合金制成,与碰撞相关带下陷空腔的结构件,由于要求具备很高的断裂伸长率,需要进行热处理。B. Fuchs等人在其文章中描述了一种调整过的热处理过程,盐芯在进行热处理时保留在工件内。这一有可能完全省略掉外包过程的美好前景,具有巨大经济方面的潜力。
S. Desrosiers等人通过考察压铸结构件的热处理性和可焊性,研究了各种不同的铝合金。所有四种进行测试的合金Silafont-36, Aural-2, Mercal-loy(367) 和 Mercalloy(368)都满足设定要求。M. Hartlieb 和 R. Donahue在其文章中说明了单个合金元素在用来加工结构件Mercalloy合金家族中的重要性。
M. Wang等人通过使用ThermoCalc模拟技术来降低合金A380(类似AISiOCu3(Fe))中的Alpha-Al-Fe-Si相和Be-ta-AI-Fe-Si相。为使Pi-Al-Fe-Si相的形成保持在少量状态,建议锰含量在0.35%到0.5%之间,镁含量小于0.65%。
铝具有两个相互关联的特性:从大气中摄取水分,并且立即转化为氧化物。K. Kendrick等人使用位于博尔肯的福士科(Foseco)公司的熔液处理站,用特殊的净化剂来降低浮渣量和金属损失量。通过这一设备,熔液纯度得到改善,而从有利于改善流动性和供料能力,以及充填性能,这样就有助于降低孔隙率。
镁合金
K.-P. Tucan等人通过一个特殊制成的压铸模来研究镁合金的热裂倾向。在模具中设置了所谓的热点,以便在不同铸造条件下触发热裂纹产生(图2)。合金使用的是微量元素含量部分能发生很大变化的市售镁压铸合金。作为对比使用的是合金AZ91。对热裂纹敏感度产生影响最大的是合金组成成份,其次是保压时间和压射速度。
锌合金
锌压铸广泛应用于比如汽车,机械制造,以及家具和配件行业。在关系到安全性的应用中,比如拉回系统,锌压铸因其优良的机械性能为其加分不少。S. Grund在其文章中强调,符合标准EN 1774和EN 12844的质量保证基础的建立,不仅仅是产生了较高的机械性能。极高的耐用度,较高的经济性,紧公差,优良的表面光洁度以及最好的近净形生产都是伴随而来的成果。锌铸造领域的创新旨在降低用料量,壁厚和重量。
D. Winter 和 F. Goodwin报告了锌压铸合金领域的最新发展情况。合金EZAC被作为样板进行了介绍,这是一种热室合金,与合金ZA27和合金HF (高流动性)相比具有非常高的强度。
F. Goodwin, L Kallien 和 W. Leis找到了,在自然和人工老化的影响下,关于锌压铸合金机械特性的新数据。结果包括合金Z410 和 ZA8的强度特性及其蠕变性质(图3和图4)。
关于从建材中回收锌 – 欧盟范围内的资源再生和气候保护 - S. Grund在其文章中做了论述。
W. Krajewski等人研究了在添加钛的情况下,对过共晶锌合金ZA27尺寸稳定性的影响。添加钛最多至1.6%的情况下,一方面α-枝晶变小以及针状析出物形成,另一方面,尺寸稳定时间明显缩短(图5)。
铜合金
A. Bardos介绍了铜压铸合金在技术领域的应用:纯铜用于高导电性产品,而顿巴硅黄铜用于高强度结构件。压铸相对于砂型铸造,通过黄铜的高冷却速度,硅的α相过饱和,从而使得强度显著提高(表格2)。
钢材和脱模剂
I.Schruff介绍了位于德国维尔市的Kind & Co.特殊钢厂所生产的,适用于高要求结构件的热作钢。对于这些钢料,具备较高的耐回火性,耐热性,耐热冲击性和热强度这些性能的组合是非常重要的。压铸模具中要实现尽可能迅速的热传送,由此达到尽可能低的表面温度,钢料种类的热导率在这方面起着决定性作用(表格3)。
关于压铸模钢料选择和硬度确定方面的重要指标, I.Schruff在文章中进行了论述。
A. Magnacca在其文章中讨论了这一问题:关于大尺寸热作钢的韧性,贝氏体和马氏体,哪一种比较好?
作为另一个重要的材料参数,B. Horstkamp, J. Jerg 和 C. Krause提到了较低的热膨胀系数,来抵消压铸模的快速磨损。采用钨复合材料能将膨胀系数从12 .10-6降低到5.10-61/K(表格4)。
A.Hamasaiid, I. Valls 和 H. Eibisch对西班牙Collita市的Rovalma公司所生产的高导热性热作钢H11 (1.2343) 和 HTCS进行比较的研究结果显示,导热性从40 W/mK提高到60 W/mK后,对产品微观结构形成,周期时间,热点形成以及模具中的均匀热分布被证明都具有一定影响。
结构件使用低铁含量铝合金的一个问题是,铸造室进浇区域形成冲蚀孔穴。R. Donahue在其文章中详细研究了金属的物理性能,如热和温度传导性,密度,熔点,蠕变和扩散所需的特殊热和活化能。与此相关有意思的是,难熔元素钨,铌,钛和锆。
K. Namiki等人介绍了两种热作钢DH31-EX 和 DHA-World,由于其高韧性特别适用于大型压铸模。
A. Hermann 和 P. Zikmund致力于研究通过热处理参数的改变来降低压铸工艺过程中模具易产生裂纹的倾向。在研究中测试了钢料Dievar 和 1.2343 EFS,以便了解硬度改变和热处理之间的关系。在压铸工艺热循环应力期间,通过硬度特性的提高,在约570 °C时可以观察到碳化物的形成对材料特性的显著影响。
压铸模具的高热负载造成化学和研磨应力,而从导致使用寿命明显缩短。S. Müller, H. Priess 和 K. Dilger因此研究了冷流道的设计,来改善这一及其重要模具设计组成部分的效力(图6)。特别是运水孔与模具外轮廓之间的间距,以及与流体技术相关的导热性起着至关重要的作用。
卡塞尔大学材料技术研究所研究了6种不同的热作钢温度变化情况. B. Scholtes, A. Gebauer-Teichmann 和 S. Wüst开发出了一种用于热疲劳实验的热冲击试验台。温度梯度较大时,加热过程中产生的压应力可能超过与温度相关的流变极限,从而导致出现塑性压缩。冷却后重新产生的拉伸应力超过屈服极限。结果表明,与热作钢种类无关,40000个周期后已隐现出来的的宏观裂纹和裂纹网络将会实际产生。
D. Schwam 和 M. Kott-mann报道了,通过用金属粉末进行层状铺涂的直接金属激光烧结(DMLS)法,来修复H13模具钢(1.2344)的可能性。
在生产越来越复杂的产品过程中,为达到较高的生产率所需的脱模剂和塞柱润滑剂,D. Tomazic强调指出了从环保角度出发,以及对产品性能产生反作用方面所面临的一些挑战。
M. Lococo建议了确定脱模剂产品特性的四种标准实验室检测法,如热重分析法(TGA),傅里叶变换红外光谱法(FTIR),固体含量测定法和目视检查。
溶解或乳化在压铸工厂工业废水中使用过的脱模剂,不允许直接排放到公共下水道系统,否则将导致高昂的处置成本。J. Freund提出用真空蒸馏来进行净化的解决方案。净化后的水满足所有法定的排放限制要求,而且不含硬化剂。
技术
总体发展现状和趋势
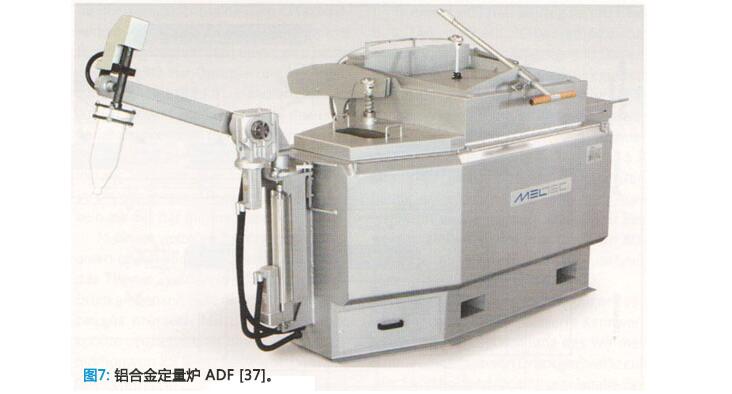
N. Erhard 和 S. Babic介绍了位于德国绍恩多夫富来公司的一系列技术革新,即富来浇注系统(FGS),真空铸造技术,和带有用来抽吸熔液的抽真空装置的铝合金真空定量炉(图7)。通过熔池液面下抽吸技术,能够确保明显降低产品中的氧化物含量,以及进料期间熔液气体去除。
使用Bühler公司的Ecoline Pro系列压铸机,在M. Fabbroni看来,就意味着能创造更高产值的压铸生产。这一系列机台的标准范围,涉及到了所有本质要求;丰富的选项使得能为高要求的生产来配置机器。特别节能的油缸能节省运营成本,并减少服务和维护费用。
针对减轻重量,不断扩展的产品功能,产品的资源再生和成本效率,以及位于瑞士乌兹维尔的机台生产商Bühler公司所诠释的机台概念和技术这些议题,P. Reichen描述了轻质金属压铸的前景。
在文章“铸造技术连接 – 纤维复合组织材料CFK和铝的结构连接”中介绍了不来梅Fraunhofer研究所IFAM在整体过渡结构领域所进行的研究活动。
压铸过程包括很多可能对产品产生影响的参数。K. MacKenzie, J. Jekl 和 J. Auld将浇口系统参数浇口厚度,浇口长度和扇角(图8)设为变量。用MAGMA软件进行模拟,结果表明,为了得到最理想的浇注产品,浇口应大一些,而浇口长度应短一些。
关于这一点,D. Gaddam, R. Gutierrez 和 K. Bisset[44]还研究了浇口几何形状对于化学反应(焊接)和对模具侵蚀的影响。
在压铸生产过程中,经济性,质量和生产率这些特性本质上是由模具确定的。考虑到它们之间的相互作用,S. Findeisen 和 H. Schulze-Niehoff开发出一种整体方法来对经济效率进行了优化(图9)。可以采取优化措施的领域是运水设计,材料,结构以及铸造技术设计。特别是内部运水中的热流量要大于外部运水。
在S. Findeisen 和 H. Schulze-Niehoff 的另一篇文章中探讨了,在压铸过程中借助壳模来减少周期时间这一课题。这一方法被证实,能够在确保工艺可靠性的前提下,将周期时间缩短23%(图10)。
R. Heid等人研发出了一种用于生产薄壁结构铸件的压铸模,适合用市售的热作钢种类1.2343进行基准测试。结构铸造中典型的损坏情况被记录下来,并进行定量比较评价。
在R. Heid 等人的另一篇文章中介绍了对铝压铸永久模损坏情况的一些预测。热裂纹和冲蚀纹为典型的结构铸造损伤类型,在铝合金中铁含量低于0.15%以及较高流速的情况下经常出现。为了证明软件模块能承受一定负载的效力,还附加比较了一款非典型结构铸造产品。
S. Müller, H. Pries 和 K. Dilger确定了用于精确计算压铸模内热流量的,基于模拟实验的参数。可达到热流量实际计算中至关重要的是运水流道中的流速,而这又主要取决于与流道几何形状相关的压力损失。在第二部分中指出了具体的可能性,模具内部运水系统中的热流量如何通过使用Ansys CFX进行数值流体模拟来进行计算和优化。并进一步研究了一种可能运水设计的三种变化情况(图11)。
F. Voltazza在迈格码软件(Magmasoft)的辅助下设计和制造压铸模,并阐明了,压铸模温度平衡如何通过关键模具区域有针对性的温度调节来进行优化。
压铸技术
如果压铸件上的倒扣能够不通过模具中的行位或是抽芯来进行加工,压铸工艺的界限就会变得清晰。L. Kallien等人在其文章中提到,在3D自由成型研究项目的研究成果中展示了- 根据三种工艺技术制造的压铸中所需要引导介质的流道:金属中空套管浇注,用水融性盐芯进行包覆成型以及通过气体注入技术进行容积挤压。这里所使用的盐芯也是通过压铸来进行生产的(图12)。
美国不伦瑞克的水星海事公司(Mercury Marine)已经使用盐芯超过40年的时间,当时是为了制造一个200马力的六缸发动机。有关现有密度值的收缩行为,R. Donahue 和 M. Degler研究了不同系统的(溴化钾,溴化钠,溴化锂,溴化铯等)盐混合物。同样对于离子结合盐,不同原子的原子直径被用来考量是否适合作为压铸盐芯。
L. Kallien, T. Weidler 和 M. Becker研究了用于加工,用带气体注入技术的热室工艺所生产的镁压铸件上中空结构的可能工艺参数。安全联接的设计是一个大的挑战,这一联接必须阻止氮气被引入到坩埚中(图13)。与铝合金相比,镁合金基于体积较低的熔化热要求对气体引入的起始点进行特别精准的控制。
P. Hofer 等人研究发现了局部冷却和再次增密对压铸件结构特性的影响。在目前正在进行的一个研究项目中,在铸件质量,结构特性,工艺可靠性,以及虚拟工艺开发数值方法的改进方面,对工艺技术可能影响因素的系统化定量和定性表征进行了观察研究。为了复制实际条件,将一套压铸模做成了双重模 - 在一次铸造过程中加工了一个试样和一个基准体(图14)。
在位于绍恩多夫的富来公司的工程技术学校中,测试了用于镁热室压铸工艺的FGS技术。FGS技术进一步去除了到目前为止都在使用的浇道系统,熔液没有任何热损失,非常接近产品的被引入型腔。N. Erhard认为这一技术具有较高的能源利用率,减少了循环物料,通过减少进气提升了产品质量,以及较高的生产率等一系列优点。
除了改善压铸模的耐用度,合适的热学设计对于铸件质量也是至关重要的。E. Ambos 等人以自动变速器上的一个阀体为例,使用了喷射冷却法,以便能对热高负荷区域,比如内核镶件,进行局部冷却。这一技术应用和实际效果的详细描述已经详细讨论过了。
R. Heid等人介绍了铝结构压铸中,近外轮廓运水设计的一种新方案。通过附加的生产工艺,在压铸模内模镶件中加工出运水的几何轮廓,这不仅能使模具运水达到理想效果,更重要的是可以显著改善运水流道中的流动模式,和所成型产品的冷却行为。在这一研究的第二部分中,作者R. Heid等人通过软件模块来预测损伤情况,特别是铝压铸永久模中的气蚀损伤(图15)。用模拟技术进行实际调整显示,对于气蚀损伤有进一步研究发展的需要。
R. Kind关注的是以模拟为基础连续模具调温的可能性。在不同设计的运水流道中,研究了传热速率,流量中断间隔时间,钙化行为以及体积流量等参数。
为了得到对压铸过程中喷雾作用的准确全面认识,按照C. Kim 等人的观点,必须将通过模具分型进行对流散热考虑在内。
在生产条件下一次复杂的铸造试验中,E. Ambos 等人研究了超过20种过程参数对一个复杂压铸件质量特征的影响。由此可以推导出,对压铸模温度进行引导控制,能够对孔隙体积和孔隙位置产生决定性影响。
对于使用这两种镁压铸合金AM60B 和AZ91D,X. Wang 等人测试了通过液压挤压,进行后续再增密的真空辅助模具,填充方法的应用情况。产品为一条轮缘,镁制的重量为2.6公斤,而铝制的重量为3.5公斤。
在设计压铸模中用阀门或辣椒形阀块进行真空辅助排气时,不仅时间、框架条件,而且真空容器中的真空度都必须包括在计算内。C. Huang 和 W. Bishenden建议,为达到最佳排气效果,在低于临界值第一阶段降低铸造活塞速度,或者在第一阶段期间中断活塞运动。
S. Bergeron 等人介绍了45度角倾斜的铸造室有利于减少铸件孔隙率。
凭借屡获殊荣的组合式内模镶件技术,为达到一贯的轻质结构的目标,使铸造厂加工复杂流道和倒扣成为可能。S. Rupp 和 F. Heppes介绍了做这种铸造镶件的不同材料,并指出这一技术的优点是,泄露风险较低,减轻重量,有可能达到最优的运水冷却效果。
B. Fuchs 和 C. Körner观察到了压铸过程中,保压大小和盐芯变形之间的关联。并且研究了以氯化钠为构成基础的,压制和烧结制成的这两种不同的盐芯类型。在保压由300bar改变为800bar后,相关的盐芯变形程度由3%上升到8%。
M. Fabbroni报道了位于瑞士吾兹维尔德Buhler公司在盐芯技术领域的最新发展状况。
铸造缺陷
为对与过程相关的变形进行预测和优化,需要对压铸过程进行模拟辅助分析,为此C. Thoma 等人正在寻找针对两种不同规格合金的解决方案。对于天然韧性产品,通过模具外形可以实现变形补偿。对于热处理过的产品,使用相应的存储位置,将铸造材料与温度相关的蠕变行为引入这一位置。这两种情况都可通过模拟辅助进行优化。
E. Ambos等人和致力于通过快速计算机断层成像来确定压铸件由孔隙率所导致的产品缺陷。在他们的文章中介绍了以医学扫描仪所用技术为基础的螺旋线CT法(图16)。一次检测所需时间在20秒到100秒之间。检测过几百个不同的压铸件,无一没有缺陷。
在L Hagner 和 F. Mnich的一篇文章中描述了快速计算机断层成像的实际应用情况。
E. Ambos 等人和介绍了快速计算机断层成像在压铸厂使用的最新成果。
周边设备和集成化
G. Rau以减震支柱罩为例,说明了由8个单独部件组成的焊接结构件,怎样通过高度集成的压铸件来取代。这样一来,整车重量可以减轻约11公斤。
J.-M. Segaud介绍了在对车身工艺链中,高效轻质结构压铸应用的整体观察中,汽车制造商宝马公司的一些相关做法。对于关键因素,材料和模具,特别探讨了喷雾和运水技术,因为其会对生产率和模具寿命产生影响。
J. Rose, A. Gebauer-Teichmann 和 B. Scholtes阐明了压铸过程中,传统喷雾技术和微喷雾对于散热和分离层形成的影响。通过在与模具表面间距分别为1,3,6和12mm的情况下测试所得的温度时间变化曲线,来计算模具表面的温度变化情况(图17)。模具起初温度过250 °C,经过3秒传统喷雾后,表面温度达到128 °C,而经过微喷雾则达到187 °C。喷雾时间小于1秒会导致研究没有任何意义。
M. Viedenz, R. Hillen 和 P. Reuther报道了德国史杰克西集团运用最新的铝熔化和定量炉技术开发出的PurEfficiency系列产品。运用这一技术,可减少材料损失和能源消耗,同时显著改善定了量精度。
按照R. Simon 和 R. Kendrick的观点,泵转子优于不带泵的转子,因为熔液可以更好的混合。转子在其整个生命周期内都会持续损失其性能。因此必须在处理时考虑到这一损失。另外他们还描述了转子形状对与磨损状况相关排气效力的影响。
位于弗里德贝格的ABB自动化公司开发出了第一套用于操控压铸设备的完整软件。G. Trommer在其文章中探讨了开发机械抚育解决方案软件包的可能性,以便为用户提供丰富的预置功能和程序。
慕尼黑aic-regloplas公司的T. Dreier展示了一种模具运水方面的巧妙方法。压铸中最重要的因素是温度,特别是内模,表面以及载热介质流出和回流温度。工艺优化的关键,是对热传递起决定作用的体积流量数据收集和分析。
F. Dorner 和 D. Hofmann强调,次品中很大一部分是由不正确调温引起的,并介绍了位于德国戈洛斯惠尔斯多夫的奥尼调温技术公司,通过多循环运水和脉冲冷却,来相应的对温度进行调节的最佳运水方案。
D. Baumgartner展示了位于瑞士圣勒日的方达瑞公司在真空设备应用方面的创新技术。
能源和资源利用率
相当长一段时间以来,位于绍恩多夫的富来公司就一直致力于研究关于压铸工厂能源利用效率的问题,K. Kerber和 K. Kerber, 以及M. Wahl 和 K. Stoltidou介绍了在能源需求记录和降低能耗措施这些领域的专业活动。在对生产工序进行检测时,压铸工厂数量众多的机台设备证明了存在基本负载消耗的情况:在压铸过程中,仅有少量工序的机械运动同时运行。
关于能源和资源效率的问题,C. Herrmann, T. Heinemann 和 S. Thiede专题报道了由BMBF资助的项目ProGRess。在这一项目中,对能量密集的铝压铸创造价值链,通过集成使用模拟辅助方法进行了审查和设计。在材料流模型的帮助下,通过各系统层面不同措施的组合,被证实节能潜力超过14%。
S. Gursky阐述了如何利用智能压铸自动化来节省能源。熔液温度的细微变化,以及坩埚炉的盖子都能够帮助节省大量能源。在一家没有经过改进的铸造工厂中,待机状态下所需能源最多占到所消耗能源的40%。位于德国奥伯恩堡的徕斯机器人公司多年来一直领导进行相关的研究工作。
压铸模拟
J. Müller 等人介绍了一种用于压铸工艺中,模具喷雾过程建模的创新方法。在模拟过程中接近现实喷雾过程的图像形成,是对压铸模的热预算进行计算的基础。在此基础上,在应力,变形和凝固模拟过程中会产生新的潜力,因为模拟需要模具的热前提条件,特别是模具运水的设计方案。
C. Thoma 等人研究了通过数值拓扑优化来进行压铸浇口设计的可能性。这样既可以消除流体分离现象,还可以通过提高气体吸收和节省铸造材料来极大影响产品质量。
以一根压铸而成的纵梁为例,K. Weiss, C. Honsel 和 R. Vomhof展示了通过模拟对机械性能进行预测的可能性。对于抗拉强度,已被证实模拟结果和实验结果高度一致。
R. Hilbinger 等人比较了在第一阶段铸造室中波纹形成的模拟结果,和一块板形部件的实验结果。在所有情况下,最佳密度值都可以在铸造活塞速度为0,7 m/s时达到。
在生产屋顶支架时,通过压铸件与塑胶一起注塑实现了所要求的产品特性。M. Fuchs以这一产品为例,阐述了铸造过程模拟的具体应用。
S. Hachtel, P. Duwe 和 0. Brunke在其文章前面部分介绍了使用高自动化3D计算机断层成像技术,来进行产品鉴定和修模的情况。
新的发展趋势和技术
压铸过程中的主要问题 - 孔隙的出现 - 按照N. Gerth等人的观点,是关系到次品率的核心问题。生成式制造技术,使得使用激光熔融的模具镶件成为可能,因为近外轮廓运水是一种尤其有效的运水设计方案。在所提到的实践研究中,密切观察了两种不同的运水设计方案(图18)。
U. Richter, K. Eigenfeld 和 R. Miksche以销钉冷却为例,解释了近外轮廓运水设计的应用。通过近外轮廓运水设计方案(激光熔融工艺),与传统的针迹冷却相比,能实现高出超过4倍的散热效果。
S. Findeisen 和 H. Schulze成功实现了通过运用壳模技术优化压铸模,来明显降低周期时间。壳模概念满足对大的传热面积,和运水与铸件之间小的间距的要求(图19)。在确保工艺安全性的前提下,被证实周期时间能缩短超过20秒(23%)。
概论
2013年在阿伦举办的铸造学术讨论会上,以幻灯片演示的形式讨论了以下论题:通过气体注入和使用盐芯来压铸中空结构(L. Kallien),压铸中的含铁过共晶硅铝合金(A. Baesgen),压铸能源效率(T. Stock),欧盟新的压铸工艺优化项目(M. Winkler), CCSME - 总结报告(W. Leis),通过在第一阶段的背压来实现低涡流模具填充(V. Scholz),以及在热室工艺过程中通过气体注入来生产镁结构件(M. Becker)。
2014年在阿伦举办的铸造学术讨论会上探讨的是如下论题:压铸模喷雾时总的热管理(L. Baraldi),铸造工厂的能源效率(R. Schillig),铝制结构和底盘部件(E. Feijen),通过结构设计标准化使质量和压铸工艺的竞争力最大化(F. Voltazza),2014国际压铸竞赛 - 获奖者(J. Schäfer),镁压铸的发展情况(T. Weidler),盐合金的热机械数据(S.Momper),挖掘数据来优化压铸工艺(M. Winkler), StaCast -欧洲研发项目成果(W. Leis),通过在热室工艺过程中注入气体来制作中空压铸件(M. Becker),压铸过程中的创新传感技术(T. Feyertag),以及不同锌合金蠕变过程和老化情况比较(W. Leis)。
回顾第57届奥地利铸造会议,可以查阅到的在压铸领域的演讲摘要,比如研究局部冷却和再加密对压铸件结构特性的影响,压铸模所使用的镁合金和创新性高性能热作钢的热裂纹倾向比较,合金和热处理对气缸盖热机械特性的影响,以及生产汽车高负载部件压铸工艺的潜力。
D. Schulz和 I. Rau对铸件净化进行了研究报道。
在2014年国际铝压铸竞赛中获奖的铸件可以在了解到。这一获奖铸件是宝马兰茨胡特工厂生产的宝马i3车型上的后桥托架。在第5届锌压铸竞赛中,获奖的是支撑轨道上PC工业控制系统中的一个组件。
G. Röders从完美设计的模具中看到了在当今世界全球化背景下,压铸行业发展的大好时机。
J. Doboro-ski对压铸行业中真空技术的应用进行了研究报道。
M. Belte 和 D. Dragulin探讨了对铝压铸工艺进行