文:黄奇德 德宝压铸技术公司
真空辅助排气工艺在铝合金压铸越来越流行。
在解决压铸件含气的问题上,国内早在二十年前就开始从国外引进真空阀压铸技术,但是发展很快受到了挫折,主要有以下原因:
1.成本太高。据估计,使用真空的成本平均占销售价的10%,个别产品会达到30%。
2.可靠性不高。与成本和效率是联系在一起的,停机造成效率降低,成本增加。很多厂家都认识到使用真空的好处,但买了一两套,最终因太麻烦而放弃,设备闲置。
3.不能体现有效性。有时发现用不用真空一样。压铸产品各异,废品原因各异,真空方法繁多,操作水平不一,这就要求正确有效地使用真空。
压铸件气孔问题
在压铸充型过程中,有很多机会卷入空气,如慢压射时料管中铝液的翻滚,喷离型剂过多令水分残留在型腔内并随后遇铝液而气化,冲头润滑油遇铝液分解气化,铝液通过浇口的高速喷溅自然和空气混合,充型过程中多股铝液撞击,都使铝液内混杂空气。同时由于高压状态下,模具的密封性高,排气口很小,使型腔的气体不容易逃出,如果浇道和排气口不合理,铸件的含气量会很高。缩孔的成因虽然和含气无关,但会因气体的混入而加大。
压铸件的内部含气会导致很多问题。特别是温度升高了,铸件的强度随之降低,而铸件内部气泡压力则上升,从而造成起泡。在远离浇口的位置,像接近排气的位置,由于压力传递较差,致密性较低,特别容易起泡。这些情况对需要加温后处理的外观件影响特别大。
近年来,由于汽车的轻量化发展趋向,更多的使用铝铸件。新一代的铝压铸件需要能热处理和焊接,这些铸件必需是不含气孔,或者含气量要低于1cc/100g。一般压铸件的含气量在10-50cc/100g范围。因此,真空压铸是重要手段。
附图是典型的模腔真空曲线。模腔内空气压力的下降速率是取决于真空泵的功率、抽气面积和漏气面积。抽气面积越大而漏气面积越小,下降速率越高,可达至的型腔真空度越高。当真空阀关闭了,由于内外气压差,外部空气迅速进入型腔,漏气面积越大,气压的恢复速率越高。因此要达至良好的真空度,除了真空泵功率大和抽气面积大外,也要控制漏气面积,特别是真空阀如果在充型完成前提早关闭,恢复速率很影响最终型腔真空度。
典型的型腔真空度曲线
常用的真空阀
真空压铸阀可分为几大类:
1.机械截至阀:真空阀打开后,靠到达的铝液冲击力关闭连杆的抽气口(图)。这种方法的好处是充型过程中全程抽气,而且抽气面积越大,效果越好。缺点是机械滑动部分使用时间长了会受油雾、铝液飞溅影响,关不住抽气口而导致堵塞和造成损坏(图),降低了使用的可靠性;因此要经常清理来保持良好工作状态。
2.时间(位置)控制关闭阀:为了避免阀块堵塞,抽气口提前关闭。一般在二速切换点或之前。优点是生产较稳定,但由于还没有充型完毕就停止抽气,型腔的真空度迅即上升,因此真空效果比不上机械截至阀。特别是密封性较差有滑块的模具。
3.平面式搓衣板 :最常用的方法。由于生产成本低,使用简单,应用非常普遍。缺点是抽气面积小,而且投影面积大,和机械截至阀相比,效果较差。只能用于真空度要求不高的铸件。
平面搓衣板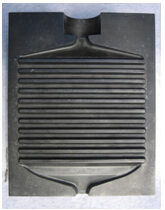
新概念真空排气块-CASTVAC
Castvac开思特三维真空排气块是由澳洲科学研究院CSIRO的王来华博士所发明的。它的诞生源于澳洲客户对使用机械截止阀过程中经常出现的堵塞和频繁保养的问题,严重影响生产效率。客户向CSIRO提出要求开发更好的真空阀,希望提高可靠性,同时不能影响抽气的效率。经过理论推断并且无数次实验和测试修改,成功的开发出目前的产品,大大提高了生产效益。
机械阀的问题主要来自作动部件,要提高使用的可靠性,最理想是避免使用可动的零件。其实传统的排气块结构(平面式搓衣板),使用简单又少维护,只是抽气面积太小,除非同时用4-5个排气块,不然就达不到机械截至阀的效果。开思特的新思路是使用三维波浪设计的排气块,这样就可以在很小的投影面积下,达到大面积的抽气效果。
通过大量的生产数据和经验,证明开思特抽气效率(气压下降速率)和机械截止阀一样,比起平面搓衣板的抽气效率高很多(在真空阀打开1秒后,平面搓衣板的真空度只有-700毫巴,而开思特已有-900毫巴,接近稳定值),而且达至的稳定真空度也更低。
在实际的生产试验中,也验证了它的效果和机械阀效果一样。
此外,开思特的三维波浪结构令开模时,金属在阀体内形成W型的折叠结构,较容易一体成型,不像平面排气块那样脱模时容易碎裂。金属沿主要冷却面的切线方向脱出,不易粘模。 而且主冷却面始终保持关闭,比如当合模面因飞料而使平行面打开0.2mm,主冷却面间隙增加少于0.02 mm 。
成本效益
以1600T的压铸机为例,按照附表成本计算,设机器使用成本(包括人工)每小时1500元;每次换阀时间半小时+机器预热15分钟,每次停机成本1125元(1500x0.75)。设二次熔炼成本每公斤0.8元,每次停机要损耗10模次,铸重15公斤,10模次的重熔成本约120元(0.8x15x10)。故每次停机换阀的成本1245元(1125+120)。机械阀容易堵塞,需要定时清理以保持生产顺畅,每天平均清理一次。按每年生产50工作周,每周6天,每年用在换阀时间的总成本高至37.35万元(1245x50x6)。另一个明显成本是阀的维护。设每次清理阀件和管道需要1.5小时,模修工每小时成本50元,这样每年的维护成本就要50x1.5x50x6=2.25万元。加上阀和配件的费用,算5000元。按寿命20万模次计算,每半年约用1个阀,每个阀15
,每年的阀体成本7.5万(15x0.5),每年使用总成本为50.6万。从附表的数据,可以看出停机是真空压铸成本的主要组成。客户也可使用自己的数据来评估。
如果用开思特真空排气块,清理维护次数大大降低,可縮短为每周一次。故每年的停机换阀成本为62250元(1245x50)。由于不用拆开清洗,每次清理阀件和管道省时,需时30分钟。每年维护成本50x0.5x50=1250元。总额是63500元,使用成本大大降低。
产品规格
开思特真空排气块有不同的规格,适合不同大小的模具和压铸机型,并已申请了发明专利保护。MV系列排气块能和目前通用的机械截止阀尺寸兼容,同时内置冷却管道和顶出机构。
CV系列使用顶出板顶出工件,定模侧也有内置顶出机构。除了标准型号外,也可按客户要求订制,包括不同尺寸,或耐磨表面处理。
要充分发挥开思特排气块的特点,公司开发了专用的控制柜。特点包括独有的试模专页,可模拟不同参数变化,测试现场不同的参数组合,方便在正式生产前验证可达的真空度,优化压射参数,并能实现双抽操作,配合多个不同位置,如不同阀体或料管的非同步抽气。可选择机械阀或排气块操作。其他功能包括:
- 8" 触摸式彩色屏幕
- 20个预设产品参数菜单,
- 低真空度报警
- 在线事故诊断和指导
- 中文,便捷的操作界面
- 过滤器和排气通道堵塞报警
- 精确的型腔内真空度的测量
- 真空运行状态的记录和显示
- 实时监控各种生产数据
料筒的密封性
汽车结构件生产时要求的模腔真空度很高(<50毫巴),除了要有高效的真空阀,和模具要有很好的密封性外,料筒的密封性也很重要。由于结构件的铝液生产温度高,又是大型模具,料管的生产温度会达到300C或以上,很容易变形。温度变化也影响料管和冲头之间的空隙控制,导致漏气和真空度损耗。要减少温度的影响,料筒最好用模温机来控制温度,以避免变形。同时也要保证冲头的冷却效率。
使用有弹性铜套和钢环的冲头可以提高料筒的密封性。当然一体化料筒是必须的。此外,冲头油的挥发也会增加铸件含气量。必须用最少的剂量,和高质量的冲头润滑油,这样可以减少气体挥发。还有更好的方法是避免在压射前投放冲头润滑油。做法是在模具打开后,冲头顶出铸件和后撤时使用喷雾式润滑。这样就完全消除润滑油挥发进入型腔。
总结
真空压铸在当前汽车压铸件生产占有越来越重要的位置。压铸结构件更要求接近零气孔的质量,来进行后续的T6热处理或焊接等工艺。此外,要实现工艺使用的普遍性,需要降低其整体生产成本,包括真空阀成本、容易使用和高稳定性等;特别是大型压铸件的生产,停机时间对生产成本的影响很大。长期的生产使用经验证明,开思特真空排气块比普通的平面搓衣板的抽气效率高出4-5倍,比起机械阀更容易保养和使用;令高真空压铸更容易实现。我司亦提供高真空压铸所需的配件,包括温度控制的料筒、模温机、带密封环的冲头、特殊冲头润滑装置,还有用户定制的模具真空管道设计、模流分析、使用技术支持和售后服务。如需进一步了解,请和我司联系。