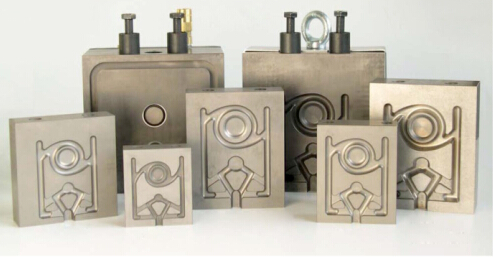
文:王福杰 余效平 张浩 马建国 贺伟 陈 仁
重庆长安汽车股份有限公司江北发动机工厂
摘 要:介绍真空压铸的的特点、优势,机械真空阀的结构及原理。对压铸生产中常见真空系统故障进行梳理,总结出相应的故障解决措施及真空系统的使用经验。
关键词:压铸;真空;故障
引言
近年来铝合金压铸件,以其高生产效率、自动化生产以及卓越的表面性能,迅速应用于建材、汽车,机电、航空等行业,其中汽车行业尤其突出。随着汽车轻量化的发展以及环保、安全等发展方向,越来越多的汽车零部件开始使用有铝合金压铸件,使得压铸工业呈现出更加广阔的发展前途;同时产品结构更复杂,成品率也要求更高,这无疑对传统的压铸工艺提出了更为严峻的挑战。
1 真空压铸技术
1.1 传统压铸
压铸是压力铸造的简称,是将熔融状态或半溶融状态合金浇入压铸机的压室,以极高的速度充型,并在高压力下完成铸件成型冷却的高效率铸造方式。高压和高速是压铸充填成形过程的两大特点,也是压铸与其他铸造方法最根本的区别所在。
压铸与其他铸造方法相比较有以下优点:
(1) 铸件的精度及表面质量较高,可压铸出形状复杂的薄壁件或镶嵌件;
(2) 生产效率高,易实现机械化和自动化;
(3) 铸件一般加工量很小或不需再进行机械加工而直接使用;
(4) 可以铸出螺纹、线条、文字、图案和符号。
压铸生产过程中,金属液以高速喷射状态充填型腔,型腔中的绝大部分气体来不及排出而被高速铝液卷入并包裹,随着铸件冷却凝固,气体开始析出富集,最终以气孔形式存留于铸件内,主要表现形式是加工后皮下气孔,如图 1。
图1 压铸皮下气孔表现
铝合金压铸件的应用范围常常受其力学性能的限制,为提高铝合金压铸件的力学性能,可采取热处理等方法,但铸件含气量过高限制了铝合金压铸件的可热处理性。同样铸件含气量过高也影响了铸件的可焊接性,根据图 2 可以看到普通压铸零件含气量.这一不足在很大范围上限制了压铸件在重要或大型复杂的受力零部件上的应用。
铸件中气孔缺陷主要有三类原因导致:一是,压射过程中来不及排出的型腔和压室内的空气 被 高 速 铝 液 包 裹 ( 一 般 充 填 时 间 在lOms—100ms);二是模具涂料、冲头润滑油遇热蒸发反应产生的气体;三是铝合金中溶解的含有大量的氢,在凝固过程中析出。
针对三种产生气孔的原因,可以采取以下措施以避免:
针对涂料蒸发气体,可以通过选用环保性,发气少的涂料并减少涂料用量明显改善;
针对铝合金溶解的氢气,可以通过控制回炉料的使用及铝液精炼除气等手段大大的减少气体含量,降低铸件气孔风险。
唯有铝液卷气,传统排气设计难以起到作用,高速充型过程仅靠铝液对气体的排挤作用难以排除,同时气压过大还会阻碍铝液的充型造成气阻。由于传统压铸工艺难以解决卷气问题,使得型腔和压室内的空气成为压铸件最主要的气孔来源。
1.2 真空压铸
为了解决压室和模具型腔的气体问题,被动排气已经行不通了,各压铸厂家开始考虑使用主动排气方式,来提高铸件质量、减少铸件气孔率。从上个世纪六十年代国外厂家开始使用罩式真空装置来实现真空压铸,通过几十年的发展近年来应用比较多的有两类真空压铸方法。一类是激冷排气槽法,另一类是真空阀法。激冷排气板法是采用通道很薄、宽大的搓板状激冷排气板,外连接真空泵或真空罐,当合金液流入排气槽时会迅速凝固堵失去流动性,不致合金液进入真空管道,如图 4。这种形式结构简单且成本较低而得到广泛应用。但是一般冷却块为了增大金属冷凝的机会防止堵塞真空管路,最顶端的间隙通常设计成 0.2 毫米,所以该形式排气气能力远远小于预想,且真空度波动较大,稳定性差。
真空阀法是采用专有的机械真空阀,装在模具的分型面上,利用合金液流动的冲击力使阀芯关闭,如图 5。瑞士 Fonderax 和日本宇部的 Gas free 真空装置都属于这一类。真空阀法具有真空度高、稳定、排气道设置灵活的优点。是目前国外推广应用最广泛的真空压铸辅助系统。不足之处是真空阀必须定时的维护,真空阀芯磨损消耗较多,成本较高,系统的使用对人员素质要求较高,并且设备的购置和后期维护费用都较高,这些方面影响此系统在国内的广泛使用。
2 真空压铸的技术优势
真空压铸相较与传统普通压铸有以下优势:
(1) 能进一步减少压铸产品内部的气泡,提高金属溶液的密度,提高产品的强度,韧性等性能;
(2) 进一步提高金属液的流速,利于充填异难铸造的部件;
(3) 更大幅度地减少铸造压力,小机台能生产大铸件,也能延长模具和压室压射杆的寿命:(4) 很好地提高了压铸件的焊剂性能,同时也可以使如电镀、氧化着色、热处理等工艺变得容易。
笔者所在的工厂先后使用了激冷排气板式真空系统与真空阀法真空系统,两相比较排气板结构简单、维护方便,但是排气效果不佳;真空阀法所用阀芯尺寸要求较高,维护成本较高,但是排气效果好且稳定。为了更好的质量,笔者最终选择使用真空阀真空系统,通过减少铸件气孔缺陷,产品成品率提高到 95%以上,产品不浸渗一次性合格率从 30%-40%提高到 90%以上。