工艺篇之一:半固态镁合金注射成型技术
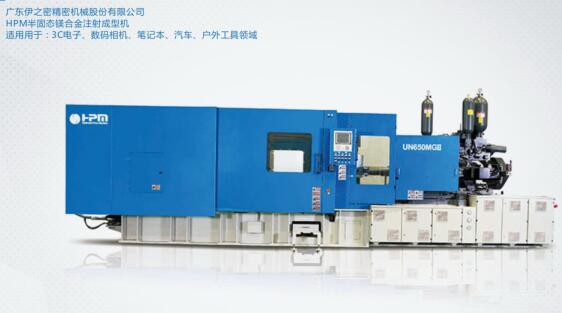
编者的话:
在中国压铸行业中,镁及镁合金,以其独有的特性和作用,已经并继续影响和改变着人们的生活。为使人们对镁和镁合金及压铸有一个较为全面、系统的了解,本刊收集、整理相关资料,从绪论、材料篇、工艺篇、应用篇四个方面简编成《中国镁合金压铸行业分析报告》,以期能为业界各位同仁工作学习带来些许便利。由于自身认识水平、工作能力有限,加之资料收集的局限性、不完整性等客观条件的限制,难免有这样那样的不足,敬请海涵并指证,以利于改进完善。
目前,世界上有40%以上的镁直接以原镁的形式用于冶金和化工、电子等领域,其他绝大部分熔炼成工业纯镁和各种镁合金。传统的金属成型主要分为两类:一类是金属的液态成型,如铸造、液态模锻、液态轧制、连铸等;另一类是金属的固态成型,如轧制、拉拔、挤压、锻造、冲压等。
20世纪 70年代初,美国麻省理工学院Flemings教授研究发现,处于凝固状态 (固相线与液相线温度区间 )的金属材料经强力搅拌后,枝晶被打碎,生成球状晶组织,具有成形时所需要的优异性能 (即流变性和触变性 ) ,并称之为半固态成形。半固态加工是利用金属从液态向固态转变 (即液固共存)过程中所具有的特性进行成型的方法。这一新的成型加工方法综合了凝固加工和塑性加工的长处,即加工温度比液态低、变形抗力比固态小,可一次大变形量加工成型形状复杂且精度和性能要求较高的零件。因此,国外有专利将半固态加工称为“21世纪最有前途的材料成型加工方法”。
一、半固态触变注射成形技术的原理
半固态金属成形方法主要可以分为流变成形和触变成形两大类。流变成形将金属液在液相向固相的冷却过程中进行强烈搅拌,在一定的固相体积分数下通过压铸或是挤压的方式来成形;触变成形则是将由搅动设备所制备的半固态铸锭重新加热至半固态进行压铸和挤压成形。与流变成形相比,半固态铸锭的加热和运输为方便,因此镁合金半固态触变成形是目前主要采用的半固态成形技术。镁合金半固态触变注射成形技术与流变成形相比,不需要事先将原材料经搅拌成为半固态浆液;与触变铸造相比在于不需要先制取半固态铸锭。该方法集半固态金属浆料的制备,输送和成形过程于一体,解决了半固态浆料的保存输送和成形控制等问题,具有较高的生产效率。
半固态触变注射成形技术源于美国Dow化学公司,由Thixomat公司将其商业化。该法将塑料的注塑成形原理与半固态金属触变成形工艺相结合。通过加热剪切镁合金粒料,可产生含固相率60%以上的半固态浆料,系统通过温控装置使套筒内温度控制在560—630℃。剪切螺旋的平均速度为380cm/s。
二、半固态触变注射成型技术的工艺过程
将被制成颗料的镁合金原料(由枝晶镁合金铸锭制成,其组织仍为枝晶组织)从料斗中加入,在套筒中的镁合金原料通过电加热转变成半固体状态,在螺杆的剪切作用下,在套筒中半固体金属浆料形成了近乎于球形状的固体颗料。在注射缸的作用下,以相当于塑料注塑机的10倍速率压射到模具内成形。
镁合金的成形与加工方法分别如图1图2所示。
同压铸法相比,半固态方法制造的产品具有铸造缺陷少,产品的力学性能、尺寸精度、表面和内在质量高等优点,此外还有节约能源、安全性好、近净成形性好等优点。目前世界上已经成功工业化的镁合金半固态成型技术是触变注射成型技术。图3-5为冷室压铸机、热室压铸机及半固态镁合金成型机成形方法示意图。
#p#分页标题#e#
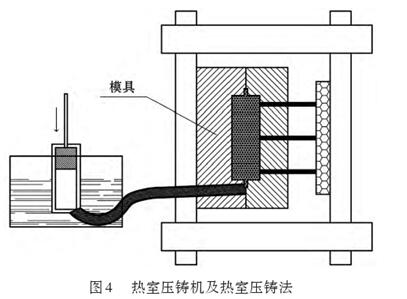
在生产应用中,历史悠久、成本低、技术成熟度高的热室和冷室压铸成形在各种镁合金成形技术中所占比例最大。镁合金压铸需要极高的压射速度,因而在模具内不可避免地会有金属液紊流及卷气现象发生,造成工件内部和表面产生孔洞缺陷,致使产品强度低、无法热处理、气密性差,另外还导致模具设计困难、良品率难以控制;其次,熔化镁合金还涉及到安全和环保等一系列问题。因此,压铸镁合金产品虽然具有尺寸稳定性好、生产率高、压铸型和工具寿命长等优点,但也具有夹杂多、气孔多、成形后难热处理、尺寸近净成形差等制约镁合金产品进一步扩大应用的问题。因此对于表面质量及机械性能要求高的铸件,采用压铸法生产的镁合金产品无法满足工业要求。
半固态镁合金注射机是基于镁合金触变性而设计的,所谓触变性是指镁合金处于固-
液相区间的合金经连续搅拌后,粘度降低,很容易填充复杂的型腔,外力撤去并静止后又恢复到原来的特性。半固态镁合金注射机工作过程是屑状镁合金通过旋转螺杆的输送与剪切,同时经过熔胶筒的加热逐渐变成半固态的浆料停留在螺杆前端,当前端储存有足够的浆料时,螺杆向前注射,将半固态浆料注入封闭的模具型腔中成型。
同压铸镁合金产品相比,半固态成形产品的夹杂、气孔等缺陷少,产品的力学性能及表面和内在质量高,此外还有节约能源、安全性好、近净成形性好等优点。
尽管镁合金触变注射成型工艺具有种种优点,但是由于采用镁合金屑作为原材料,以类似注塑的方法进行生产,使得该技术比较复杂、对工艺设备的要求较高。近年来,发达国家仍然在不断开发镁合金触变成型技术,这些情况说明镁合金的半固态成型技术仍然处在不断发展之中,将会出现新的技术突破。近些年,我国在半固态铸造领域虽然也开展了较为广泛的研究,但在半固态成型技术产业化应用领域仍处于起步阶段。与压铸机的压射系统不同,半固态注射成型加工设备的注射系统在要求有很高注射速度的前提下,同时可以在几毫秒内停下来,因此,对于注射系统的控制有着较高的要求。国内外普通注塑成型机的注射速度多为0.1 m/s,对于要求特殊性能的注塑机,其最高射速也不超过0.4~0.6 m/s。而对于镁合金用注射成型加工设备,由于镁合金材料本身的热容较低,因此,为了保证镁合金能够迅速充型,获得良好的产品质量,注射速度至少应为3.0 m/s。
三、半固态镁合金注射成型技术和设备的市场应用前景
镁合金半固态加工技术采用了一种所谓“一体化”的成型方式,将压铸和注塑工艺合二为一,模具和成型材料与压铸工艺相似,工艺过程则接近于注塑成型。采用这种工艺生产的零件除具备半固态成型件的一般特点外(例如零件内部致密、凝固收缩小和精确成型),与普通压铸相比还具有操作简单、安全、效率高、切屑或碎片经碾研后回收率近100%(可免除二次精炼过程)以及更有利于环保等特点。因此,触变注射成型技术是一种面向形状复杂、高致密度零件的新一代成型技术,具有巨大的应用潜力,成为“面向21世纪的新一代金属成型技术”。应用该技术生产的产品机械性能高于压铸件、耐腐蚀能力优、模具寿命长,特别适合于薄壁产品的成型(壁厚最低可达0.5 mm)等优点;同时,具有孔洞率极低、品质精良、接近净形化成型,不需熔炼金属的设备、生产趋于更加安全以及更有利于环保等特点。利用该成型法生产的产品主要用于表面质量及综合机械性能相对较高、薄壁、精密的零部件的生产。例如,汽车、电子产品、电子仪器零部件以及其他消费类或工业产品的生产,特别是笔记本电脑、数码相机、数码摄像机、数码投影设备、移动电话、电视和监视器等镁合金外壳的制造,以及方向盘、传动装置零件、曲轴箱零件、节流阀体、发动机零件、泵壳、制动零件等汽车用镁合金零部件的生产。
半固态镁合金注射成型设备的实用范围和应用前景主要有以下三个方面:
(一)汽车工业。随着节能环保要求的不断提高,汽车工业对轻量化的要求不断提高。在国家科技部的推动下,镁合金零件已经在汽车上获得了批量应用。然而采用压铸工艺生产的镁合金汽车零件由于气孔多,力学性能差,以及无法热处理等不足,还无法成为关键的结构零件。半固态触变成型设备的出现将为高性能、轻质镁合金汽车零件的成型和制造提供有力的支持,更进一步的促进汽车的轻量化。#p#分页标题#e#
(二)“3C”产业。移动通信手机外壳,微型便携式计算机外壳等产品是镁合金半固态触变成型设备应用的一个重要领域。由于半固态铸造温度低,半固态浆料流动性能好,使得镁合金半固态触变成型方法易于制造薄壁铸件,而且表面质量好,尺寸变形小,机械性能高。目前Dell、IBM等国外著名计算机公司已经大批量采用半固态触变成型方法制造的机架、外壳等,Motorola、Nokia、Samsung等知名手机制造商也大批量采用半固态触变成型方法制造的手机壳体。国内目前还是采用热室压铸的方式生产此类壳体,存在着产品表面质量差,尺寸精度不足等诸多问题,在产品质量无法与国外产品竞争。半固态触变成型设备的研制成功将为国产手机提供一个高质量手机壳体生产的技术平台,提高国产“3C”产品的竞争能力。
(三)航空航天和国防工业。航空航天和国防工业对零件的要求首先是高性能,其次是轻量化。由于内部气孔等先天不足,压铸镁合金的应用受到限制。挤压和锻造镁合金强度虽高,但受到工艺方法的限制,难以制造复杂结构的零件。半固态触变成型设备出现将摆脱此类设备依托进口,大吨位设备进口受限等诸多问题,为航空,航天和国防工业提供高性能,复杂镁合金零件的生产方法,提高装备的技术含量。