摘 要:以大面积镁合金压铸模轮毂铸件微弧氧化表面处理为例,设计了镁合金微弧氧化表面处理技术生产线,研究了微弧氧化表面处理技术的成膜机理,以及工艺的参数对膜层质量的影响。 结果表明,微弧氧化表面处理技术用于镁合金压铸模铸件表面处理效果较好,对大面积镁合金铸件表面处理有重要参考价值。
关键词:镁合金;压铸模;微弧氧化;表面处理
镁及镁合金是目前所知工程材料中最轻的金属。 与其它工程材料相比,镁合金是金属,具有金属的特质,具有很高的比强度和比钢度,被誉为 21世纪的金属,又由于其质量轻,同一重量下生成的零件多且价格便宜,近年来在电子、汽车、航空航天等领域得到一定的发展,而且发展前景越来越好,但镁合金容易氧化,耐蚀性较差,是制约其发挥优势的一个主要因素,采用微弧氧化技术又称微弧放电氧化 (Micro-arc Discharge Oxidation, MDO)可以解决这一问题。 该方法是将压铸镁合金铸件完全浸到硅酸盐溶液内,引入脉冲电源,使其高压放电,并在阳极区产生等离子微弧放电,火花放电使阳极表面局部温度升高,微区温度高于 3000 ℃,从而使阳极氧化物熔覆于金属表面,形成陶瓷质的阳极陶瓷层,极大提高了膜层的综合性能。 但一些资料提供的工艺参数只在实验室下获得,未见生产应用,且大多只局限于小型工件范围内,如在电源系统输出电流为 100~300 A 时,一次性处理面积仅为0.05~0.20 m2。 而对于大型的镁合金工件(表面积在0.5 m2以上)进行微弧氧化时,也有相关报道,但未见生产应用效果。
1 微弧氧化技术电解车间工艺管线设计及所用主要设备
1.1 微弧氧化技术电解车间工艺管线设计
图 1 为镁合金压铸模铸件微弧氧化技术电解车间工艺管线布置图。可以看出,该工艺管线由专用脉冲电源、电解槽、电解液中间槽、换热器、冷却塔、冷却水中间槽及若干管线组成,这些设备起到储存、搅拌、流动、冷却硅酸盐电解液的作用,能保证电解槽中的电解液所需的温度并进行消电离, 使压铸镁合金铸件表面产生持续的放电,进行微弧氧化处理,最终可形成致密的陶瓷层。
1.2 微弧氧化技术所用的主要设备
自制的 MAO-400 微弧氧化电源是微弧氧化生产线的关键,为超大功率脉冲电源。正电压最大值可达 600 V, 负电压最大值可达 400 V, 脉冲频率从100~1 000 Hz 可调,正脉冲个数从 1~100 可调,负脉冲个数从 1~20 可调,占空比从 10%~90%可调,可以同时加工 3~4 个总面积达 2 m2的镁合金轮毂,总处理表面积达 8 m2,陶瓷层最大厚度达 40 μm。在调试中,设备运行比较稳定,安全性能较好,遇到意外情况可及时切断电源,达到保护设备的目的。 同时,该设备还可以对铝合金等其他金属进行微弧氧化表面处理,调试结果同样可以达到用户的要求。最终对加工过的镁合金轮毂进行质量鉴定,陶瓷层的厚度、硬度、光洁度均达到了使用的要求。
和电源一样, 也是微弧氧化技术生产线的关键设备。 电解槽尺寸为 800 mm×1 100 mm×1 600 mm,有效容积为0.9 m3, 能同时处理 3~4 个大型镁合金压铸模轮毂。 电解液的流量保持在 15 m3/h,电解槽和中间槽的总有效体积为 6 m3左右, 可以满足搅拌、流动、冷却等要求。电解液为碱性溶液,能腐蚀铁等不耐碱的金属,故选用塑料做电解槽箱体材料。工作时阳极经常吊装, 工作电压在 200 V 左右属于高压,在电极的两头安装了安全保护装置,防止触电。内部的搅拌和循环系统用来提高电解液的均匀性并起到冷却电解液及消电离。电解液中间槽同电解槽的材质一样, 工作过程是封闭的,保证电解液清洁。
冷却塔采用废弃的较大型油罐改装而成, 通过热交换器进行能量交换,再通过冷却塔进行冷却,保证电解液适宜的温度。
2 微弧氧化处理工艺
汽车工业学会对运动部件镁合金压铸铸件有质量要求,特别是耐蚀、抗磨、抗划伤性能,其次是表面光洁,基于以上要求,结合微弧氧化技术的特点,本课题组设计了微弧氧化技术生产管线, 研究了该技术的微弧氧化机理以及工艺参数, 在镁合金压铸模铸件表面生成了表面光洁的白色的抗腐蚀性、高硬度均较好的的陶瓷层。
2.1 微弧氧化机理
首先把镁合金压铸模铸件放入到硅酸盐溶液中, 采用交流双脉冲微弧氧化电源在镁合金压铸模铸件表面产生微弧放电电火花,瞬时温度达到 3000 ℃以上,直接把镁合金氧化烧结,成功的在AM 60B 镁合金压铸模铸件(阳极)上沉积出硅酸盐陶瓷层,而阴极电流可以不断地减薄膜层, 以保证陶瓷层的质量。该陶瓷层坚硬且表面光滑,既有高的耐磨性及耐蚀性能,又保持了陶瓷与基体的结合力。 与喷漆、自蔓延高温合成、铬化电镀等表面处理方法比较,克服了表面膜层致密性差和结合力不强等缺点。
2.2 研究方法及工艺流程
通过增加镁合金压铸模铸件表面微弧氧化预处理,改变硅酸盐电解液配方,调整微弧氧化技术设备工艺参数等方式, 获得硅酸盐陶瓷层的金相组织和使用性能,通过金相显微镜及盐雾试验检测,进行观察和检测陶瓷层的微观组织和表面质量。
工艺流程为: 改变电解液配方→设定微弧氧化技术设备工艺参数→镁合金压铸模铸件碱洗 (除去轮毂表面油污)→清水槽清洗→直流电源建立陶瓷层(微弧氧化前预处理)→微弧氧化技术处理(15~20 min)→清水槽再次清洗 1~3 min(除去电解液)→热水封闭 处 理 ( 温 度 80 ℃ ;15~20 min)→ 冷 水 槽 冷 却(2 min)→取出轮毂铸件→烘干→清理检查→完成。
2.3 微弧氧化技术设备工艺参数
镁合金铸件的表面积为 0.48m2,属于表面积较大镁合金铸件。 电压设定范围 80~220 V,电流密度设定范围为 0.8~1.5 A/dm2,氧化时间为 20~30 min,频率设定范围为 500~700 Hz, 占空比设定范围为15%~25%。
3 微弧氧化设备工艺参数的影响因素
3.1 电解液浓度对微弧氧化设备工艺参数的影响
改变电解液配方的浓度范围: 硅酸纳 10~50g/L,甘 油 20~40 g/L, 氢 氧 化 钠 1~20 g/L, 氟 化 钾1~50 kg/L。 随着电解液浓度增大,特别是氢氧化钠和氟化钾浓度的增大,碱性值越大,起弧电压很低,很容易产生电火花,但对陶瓷层的溶解作用也增大,不利于陶瓷层的生成。当其它成分不变时,将硅酸纳浓度提高到 50 g/L,氢氧化钠浓度提高到 44 g/L 时,电火花起弧电压只需 70 V,但工件表面出现团状的大的弧光,这是镁合金金属大量燃烧的结果,等处理完毕后,检查陶瓷层,发现陶瓷层呈花状,呈不均匀分布。减少硅酸纳及氢氧化钠浓度时,结果发现电火花起弧非常困难,起弧电压峰值需达到 200 V 以上,且加在轮毂铸件上的电压、电流的波动较大,会损坏微弧氧化电源。 经过不断的实验,总结出最佳的组成溶液浓度为:甘油 32g/L,硅酸纳 26g/L,氟化钾12 kg/L,氢氧化钠 10 g/L。
3.2 微弧氧化处理工件表面积对工艺参数的影响
为了研究工件表面积对工艺参数的影响, 在最佳的组成溶液浓度下,分别选用 0.04、0.60、1.1、1.7、2.2 和 2.9m2的镁合金压铸模铸件进行了实验,总结出以下规律: 微弧氧化技术电火花的出现前提是工件表面必须先形成一定厚度的膜层, 而且膜层的形成时间较长,大约需要 10~20 min,且膜层形成所需的电压较小;随着压铸件表面积的增大,形成膜层所需的电流也在增大,但电压变化不大;随着膜层不断的增厚, 形成电火花所需的电流和电压会产生突变, 处于一种不稳定状态。 当膜层增长到一定厚度后,增加处理压铸件两端的电压到 150 V 左右时,可以看到压铸件表面出现零星的电火花微弧放电,继续增加电压的数值,电火花微弧放电越来越剧烈,就像满天的星星在闪耀,明亮且不断的在跳动,这时,电火花微弧放电所需的电流与电压基本上呈线性比例的增大。当电压达到 180 V 时,压铸件表面出现了大量的非常密集的微小的微弧放电电火花, 压铸件表面膜层质量较好,光滑而均匀,在增加电压到 200V 左右,微弧放电电火花开始变成小的电弧光,压铸件表面出现小面积坑蚀现象, 而此时电流的增长速度则比较缓慢。再增大电压的数值,电流基本上处于某一数值不动时,表明膜层已达到一定厚度,微弧氧化处理的化学反应基本趋于稳定, 电火花又出现零星的分布,微弧氧化处理过程也即将完成。如果此时再继续增大电压数值,会出现明显的电弧光现象,且是大面积的呈现坑蚀现象膜层表面也会出现小裂纹, 压铸件微弧氧化处理后表面质量变差。 生产实践表明, 大面积压铸件微弧氧化表面处理技术最佳电规程为: 电压 180 V, 电流密度 1.1 A/dm2, 频率700 HZ,占空比 20%,氧化时间为 30 min。
4 镁合金铸件微弧氧化处理后陶瓷层结构特征及品质分析
4.1 镁合金铸件微弧氧化处理后陶瓷层结构特征
图 2 为镁合金压铸模铸件微弧氧化技术处理后表面陶瓷层表面和截面形貌。可以看出,陶瓷层是由无数微小的"小火山锥"呈枝状结合并相互交织成网状结构。"小火山锥"中心部位是细孔,大多数人认为是电解液与基体反应的通道, 也是微弧氧化电火花放电时熔融态氧化物喷出的通道。 细孔直径的尺寸大小也不相同,这是因为通过通道的电流不同所致,在直径较大的孔的周围因通过电流较大, 电化学反应剧烈而产生大量的微裂纹, 细孔和微裂纹的产生会影响陶瓷层的使用性能, 可用热水封闭处理的方法填充细孔及微裂纹。
4.2 微弧氧化陶瓷层的品质检测
4.2.1 微弧氧化陶瓷层微观质量分析
通过采用 SSM Analysis 分析软件,对陶瓷层表面致密性进行分析, 小火山锥细孔所占表面积比率为 18%,说明通电通道较多,电化学反应剧烈,生成的微弧氧化陶瓷层致密性较好。 图 3 为微弧氧化陶瓷层的扫描电镜截面形貌。可以看出,陶瓷层平均厚度为 22 μm,陶瓷层与铸件镁合金基体结合紧密,界面明显清晰且致密性较好,没有大的孔洞及裂纹。陶
瓷层从表面到基体分别由疏松层、 致密层和过镀层3 部分组成,过渡层位于陶瓷层与基体的交界面,疏松层位于表层,存在较大孔洞和裂纹等缺陷,致密层位于其它两层之间,是提高陶瓷层使用性能的关键。 图 4为致密层的 XRD 图谱。 可以看出,衍射峰值最高的是 Mg,表明铸件主体是镁合金,致密层主体相为立方结构的 MgO, 其次是 Mg
2Si
2O
4及 MgAl
2O
4
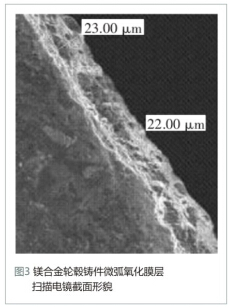
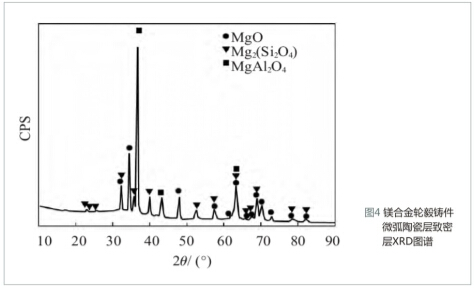
镁酸盐化合物,俗称尖晶石相,这些相表明铸件镁合金基体与硅酸盐电解液中化学元素发生电化学反应。 进一步研究显示, 尖晶石相能大大提高陶瓷层的耐磨性。 这也是微弧氧化技术陶瓷层质量优于其他表面处理膜层的根本原因。 另外, 通过热水封闭处理后的微弧氧化陶瓷层的孔隙率很低, 陶瓷层从基体上生长,因此与基体结合紧密,不易脱落,也提高了膜层的耐腐蚀性能。
4.2.2 外观及厚度检测
图 5 是微弧氧化表面处理后的镁合金压铸模铸件照片。 可以看到,轮毂表面通体白色,陶瓷层均匀发亮,手感极好,用较硬的刀片轻轻刮蹭,几乎无陶瓷层脱落。 使用涡流测厚仪亦可很方便的检测出陶瓷层厚度,具体方法是在轮毂表面不同地方取 10 个点测量,取其平均值,用该方法测量的厚度较分析软件稍微大一些,为 25 μm 左右。 以上这些外观及厚度检测都表明该陶瓷层质量较好, 能满足轮毂部件使用性能要求。
4.2.3 盐雾试验品质检测
采用盐水喷雾试验机对微弧氧化处理后的镁合金铸件表面陶瓷层进行盐雾试验发现,48 h 腐蚀率仅为 0.108%,热水封孔后仅为 0.073%,比铬化处理的腐蚀率低, 说明微弧氧化处理后镁合金压铸模铸件耐蚀性能优越。
5 结论
(1) 大面积镁合金铸件微弧氧化技术处理在电解过程中因微弧放电会产生大量的热量, 需设计生产工艺管线, 通过热交换机和冷却塔来保持电解液恒温。
(2) 大面积镁合金铸件微弧氧化技术处理最佳电规程为:电压 180 V,电流密度 1.1 A/dm2,频率为700 Hz,占空比为 20%,氧化时间为 30 min。
(3) 大面积镁合金铸件微弧氧化技术处理电解液最佳的浓度为:甘油 32 g/L,硅酸纳 26 g/L,氟化钾 12 kg/L,氢氧化钠 10 g/L。
(4) 大面积镁合金铸件微弧氧化技术处理后陶瓷层 48 h 腐蚀率微弧氧化为 0.108%, 热水封孔后仅为 0.073%,表面外观质量较高,厚度为 25 μm 左右,能满足其使用性能。