文:张海华
沈阳工学院
摘要: 根据 J1140 型压铸机压射系统的设计要求,分析压铸机压射系统增压液压原理,对增压蓄能器的容积进行计算;结合实践应用,介绍蓄能器的选择及应用方法。
关键词: 压射力; 压力; 增压; 蓄能器
压铸机是在压力作用下把熔融金属液压射到模具中冷却成型,开模后得到固体金属铸件的一系列工业铸造机械。压铸机压射系统设计要求是: 最大压射力大于合型力的 1/10; 最大压射速度大于 5 m/s; 由系统压射力增压到最大压射力的建压时间小于 40 ms。如图 1 所示,为保证压射系统最大压射力及建压时间的要求,国际通用的压射系统结构是采用压射缸与增压缸串联的结构形式。利用增压缸对压射缸内密封油进行增压来保证最大压射力要求,设计增压蓄能器来保证最大压射力及增压时间的要求。
1 J1140 压铸机增压原理分析
1. 1 J1140 压铸机增压液压原理
如图 1 所示,压射时,液压油经过增压活塞杆与浮动活塞之间的缝隙,推动压射活塞向左压射; 由压射蓄能器放油在同一油路进行快压射; 当金属液充型完成后,增压控制阀换向,增压主阀 JV14 开启,增压蓄能器内的压力油进入增压缸,推动增压活塞向左运动,使增压活塞杆与浮动活塞接触,将压射活塞与浮动活塞之间的油腔封闭,由于增压力极大,将封闭油腔内的液压油压缩,使其油压达到 32 MPa 以上,从而形成最高的压射力。
1. 2 压射力调节方法
为使压铸机能够应用在较大的工艺范围内,必需使压铸机的压射力大小能够调节。压铸机压射力由以下公式计算:

式中:

为增压缸直径,200 mm;

为增压蓄能器排油后油压力;

为压射缸内径,130 mm;

为增压活塞杆直径,100 mm;

为液压系统压力,12 MPa
由式 ( 1) 看出,在压射系统结构确定以后,调节压射力大小就只能调节增压蓄能器放油后的压力。
1. 3 增压蓄能器应用原理
为使增压蓄能器放油后的压力可调,在增压蓄能器的冲油油路上设计有减压阀 VP4。当增压蓄能器充气压力一定时,VP4 减压的压力范围有一定限度,因此,增压蓄能器的冲气压力也应该可调。当需要改变增压蓄能器充气压力时,通过充气阀充放气是非常不方便的,在液压原理上,增加对蓄气瓶冲油、放油来改变增压蓄能器充气压力。如图 1 所示,将单向阀JV15 关闭,打开截止阀 VK12,系统液压油冲入气瓶,将低压气体压缩,气体压力升高; 需降低气体压力时,将液压系统卸荷,打开截止阀 VK11,气瓶内液压油在气压作用下流回油箱,气瓶气体体积增大,气压减小。
2 增压蓄能器的容积计算
压铸机每增压一次,增压蓄能器所排出的最大油量等于在压射室最大金属浇入量时增压缸内增压活塞移动最大行程所形成的液体体积。
2. 1 增压活塞最大行程
根据 《国外压铸》,增压活塞最大增压行程按以下经验公式计算:

(2)
式中:

为增压活塞最大增压行程;

为压射缸刚性和密封渗漏系数,0. 2;

为型腔和浇道金属补缩和密实系数,0. 06;

为金属定量误差引起的增压器提前接通系数,0;

为最大金属浇入量,4. 5 kg;

为最大压射室直径,80 mm;#p#分页标题#e#

为压铸铝合金密度,2. 7 t / m3。
2. 2 增压一次增压蓄能器排出油量

2. 3 增压蓄能器最小容积计算
为减小增压蓄能器的总体结构,实际结构设计时,增压蓄能器采用活塞蓄能器与蓄气瓶组合的设计方式。增压蓄能器工作时的建压时间要求小于等于40 ms,因此增压蓄能器排油的时间极短,可将增压蓄能器内的气体体积变化过程视为绝热变化过程,这一变化过程中的气体状态符合玻义耳气体定律,即
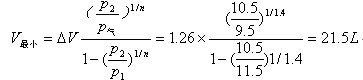
式中:

最小为增压蓄能器的最小容积;

为增压蓄能器调节最高压力,11. 5 MPa;

为增压蓄能器排油后油压力,10. 5 MPa;

为增压蓄能器最高充气压力,9. 5 MPa;
n为绝热过程系数,1. 4;
2. 4 增压蓄能器容积计算
增压蓄能器充气压力一般为 7 MPa,主要考虑充氮气的利用率 ( 氮气瓶压力 10 MPa) 。采用对蓄气瓶冲油的方法,将气体压力调整到 9. 5 MPa ( 最高) ,使气体压力从 7 到 9. 5 MPa 可调。设增压蓄能器原始充气压力

,蓄能器组合容积

。由于冲油过程较长,视为等温
根据计算结果查阅现有的蓄能器与蓄气瓶标准容积,选择活塞蓄能器为6 L,气瓶为25 L,总共31 L。
3 结论
增压蓄能器的控制油路是为扩大机床的工艺范围,并充分考虑机床用户的使用成本及使用的便利性而精心设计的,具有复杂性和典型性; 增压蓄能器的计算方法比较复杂。这两种典型设计方法完全可以应用到其他的液压系统中。