文:李实 上海博优模具技术有限公司
前言:
铝合金压铸模具在使用过程中,由于液态铝合金在瞬间填充模具型腔使得模具表面承受高温而表面温度升高。压铸铝合金产品的冷却成形是模具材料做为导热体把铝合金凝固过程散发的热量传递到模具内部。由于压铸成形的产品形状不规则,即产品的厚度不均匀,那么铸件产品在凝固过程中所散发的热量是不同的。模具设计过程中,需要有效的设计模具的内冷却水道分布使得模具表面温度差降低到最小。这样才能减少模具表面温度差异从而控制压铸产品的变形,减少缩孔的发生,保证班产量与生产节拍。
模具温度场的控制需要在模具设计的初期就考虑周全。也就是说,需要设定好班产量与生产节拍(如:60件产品/小时)从而了解模具在生产过程中所散发的热功率。在了解模具不同厚薄部分在生产时所散发的热功率后,按照图2的Monogram图表计算出冷却水道的直径,距离表面的距离,以及冷却水的流量,从而控制模具表面温度在240度。
目前常见的问题是,温度场的建立不是在计算的基础之上,而且根据经验大致估计一下冷却水道距离表面的距离,以及冷却水道的孔径。其结果是,模具表面温度难达到均匀。当模具局部有过热时,采用大量喷涂脱模剂的方法来冷却模具。这样的结果是,模具在使用很短一段时间后,如3000多模次,模具表面出现热疲劳裂纹。在其后的生产过程中,由于模具持续承受剧烈的冷/热循环导致模具早期失效达不到预定的8-10万模次寿命要求。
1. 压铸时铝合金的热量散发
压铸时,通常使用铝锭把其熔化成液态。如果有6公斤的铝锭需要熔化成730度的液体,那么所需要的热量是:6436千焦耳的热量(这里省去计算公式)。这其中包括升温需要的比热量以及固态到液态的热熔量。
压铸时,模具需要带走热量把铝合金凝固成需要成形的产品。如果把液态的铝合金成形到固态的产品而产品的温度在380度时,6公斤的铝所需要带走的热量是:4400千焦耳的热量(这里省去计算公式)。
如图1所示,这些热量的散失可以是模具内冷却水带走10-50%的热量,也可以是脱模剂带走10-50%的热量。热量散发到空气中5%左右,压铸设备带走10%左右的热量。 但是,直接把铝合金凝固的热量带走的是模具与水基脱模剂。那么在模具设计时,就需要考虑模具内冷却水带走的模具热量占的比例以及水基脱模剂带走热量占的比例。高端模具设计应当是内冷却水带走的热量多,而尽量减少水基脱模剂的喷涂。
2. 压铸模具温度场设计的计算
铝合金液体从600度冷却到固体的350度时,所散发的热量大致是1500焦耳/立方厘米。这些热量的散发,包括温度差下降所释放的热量以及铝合金热熔量所散发的热量总合。
如果考虑厚度8毫米的铸件的部分,长度是100毫米,宽度是80毫米,那么这部分铸件的体积是:64立方厘米;这部分铝合金凝固时,所散发的热量是:1500X64=96千焦耳的热量。这些热量所散发在模具表面的面积是:100X80=80平方厘米。
如果生产节拍是60件产品每小时,那么每个小时模具所接收的热功率是:60X96=5760千瓦的热功率。
根据图2的图表,如果所讨论的产品部分是平面,冷却水道如果距离表面45毫米的距离。冷却水道直径在6毫米,而且水的流量在4升/分钟时,冷却水带走的热功率是:359千焦耳/厘米。那么,需要的冷却水道长度是:5760÷359=16厘米。这样,对于所讨论的平板部分的产品需要在模具内安装2条冷却水道,每个水道直径6毫米,水流量4升/分钟,水道长度80毫米,水道距离模具表面45毫米。#p#分页标题#e#
图2中左上角的三条曲线,中间的曲线是铝合金模具表面温度在240度。右侧竖轴是每厘米长度的水每小时带走的热功率。曲线底部的横轴是冷却水距离表面的距离。举例而言,如果冷却水距离模具表面是25毫米那么其所能带走的热功率是:150千焦耳/小时。即,每小时带走150千焦耳的热量。
涉及具体产品的温度场设计时,需要把部件分解成不同的小部分来具体分析局部冷却水道的安装,并且计算出是采用直管冷却还是点冷却。对于盒子类产品,多数情况下需要点冷却这时需要具体计算点冷管道顶端距离模具表面的距离。点冷通常是直管道冷却效率的50%。
3. 借助模流分析的凝固场模拟来设计冷却水
压铸产品的形状是千差万别的,在同一个产品上有些部分铝合金壁较厚,而另一些部分就会璧较薄。通常在模具设计时,当浇注系统设计完成后,设计人员会使用模流分析来分析铝合金液体的流态。常用的模流分析软件也有速度场,温度场分析功能。借助铝合金凝固温度场分析,可以看到凝固最慢的壁厚部分其也是最容易产生缩孔的部分,如图3所示。
缩孔的产生是因为铝合金液体在凝固为固体时会有4%以上的体积收缩。 温度场设计时,可以考虑把铝合金产品的加工面的冷却加强使得缩孔部分推移到非加工面内。在图示的凝固模拟分析中,环形孔部分需要加工那么就需要考虑在这个部分加强冷却。具体冷却水道的安排需要按着第二部分讨论的计算方法进行计算:位置,水道直径,水的流量,带走的热量。
在此基础之上,计算整个模具的冷却水排布。之后,把数据输入模拟分析软件进行温度场分析模拟。同时,还需要考虑水基脱模剂带走的热量,决定脱模剂的喷涂量。理想的模具设计是尽量采用模具内冷却来把模具的热量带走,最少的使用水基脱模剂的喷涂。
因为脱模剂的喷涂会对模具表面产生热冲击。
4. 脱模剂对模具表面的热冲击
在模具使用过程中,通常模具的表面温度在150-350之间。 脱模剂喷涂到模具表面时,模具表面温度会下降形成温度差ΔT。温度差(ΔT)越大,模具表面由于温度变化所产生的热应力越高。并且应力的变化遵循以下物理学公式:
σ=(Ε/1-ν)*ΔT*α
这里:σ是热应力MPa;Ε是杨氏模量;ν是柏松比;α是热膨胀系数。
按以上公式计算,如果模具表面的温差达到380度时,热应力的大小在800MPa以上。对于46HRC硬度(1500MPa强度)的模具材料,当模具表面温度瞬间达到520度时,材料在高温下的强度下降到800MPa左右。也就是说,由于喷涂脱模剂所产生的温差已经超过模具材料的强度。这样,模具由于热冲击可以在几百模次开始产生裂纹。因为温度差所产生的应力已经超过模具材料表面的强度。
在实际生产中,通常的问题是由于温度场设计不合理,内冷却不够,导致使用大量的脱模剂喷涂模具,脱模剂的水滴从模具表面流下来。这说明模具的表面温度已经低于水的沸点100摄氏度。模具材料承受着激冷急热,模具会在实际生产几千件产品后出现大量的微裂纹。
5. 温度场设计不当案例
由于模具的型腔多数不是平板,有些产品壁厚的部分又是曲面。在模具温度场设计时,需要分别考虑冷却水道的安排并计算所带走的热量。使得模具表面的不同部分温度达到一致。
图4是汽车转向器产品在生产6万模次产品后的状态。产品的主壁厚3毫米左右,侧面圆筒壁厚5-6毫米。可以看出,模具3毫米壁厚处没有任何热疲劳裂纹。但是,产品壁厚5-6毫米处热疲劳裂纹很严重。说明,壁厚处温度较高,脱模剂在此处的喷涂量不够。长时间的使用会导致模具此部分的局部温度上升,模具表面硬度会下降,耐热疲劳性能下降。材料在此处容易出现热疲劳裂纹。
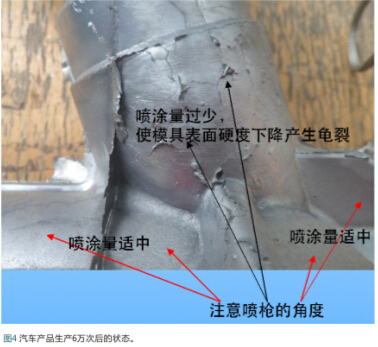
#p#分页标题#e#
为了避免这样的情况发生,在模具设计初期就需要计算厚壁部分侧滑块的内冷却水道安装。使得模具表面无论在壁厚与壁薄处的温度一致或者近似。具体的,壁厚部分铝合金部件内径58毫米,外径64毫米,长度60毫米。厚壁部分的铝合金重量是93克,抽芯的表面积是:10平方厘米。铸件的曲率半径是29毫米。93克的铝合金凝固到350度时,如果每小时生产60件产品,那么散发的热功率是:1500X35X60=3150千焦耳/小时。这些热量散发到10平方厘米的面积上。按照图2的Monogram曲线,那么采用10毫米的冷却水道在侧滑块的心部,流量在4升/分钟,每厘米长水道内的水带走的热量是540千焦耳/小时的热功率。采用60毫米长的心部冷却水道,能够把铝合金在凝固过程中把所散发的热量带走使得模具表面的温度在240度。这样,6毫米壁厚的部分就可以与其他3毫米壁厚的部分模具表面温度一致。
现在的问题是,由于没有很好的计算内冷却水的设计导致模具寿命的下降。其补救措施只有在脱模剂的喷涂上做调整。如果不考虑改变模具内冷却水的设计改变,对于复制模具,可以参考借鉴之前的模具使用情况,把脱模剂的局部喷涂做调整。对于过热的部分,多喷脱模剂使得模具表面温度尽量均匀一致。
图5 是制作缸体盖罩产品的模具。由于冷却水道距离模具表面太近,导致产品有冷隔。为了使生产持续进行,采取的措施是关闭冷却水。而模具的冷却采用大量的喷涂脱模剂。由于脱模剂冷却的只是模具材料的表面一层,而且模具会承受冷热冲击。这类模具无论采用什么进口模具材料都在3000模次以内产生龟裂纹如图所示。而相应的定模部分由于冷却水设计合理则无热疲劳裂纹。
这个案例是模具温度场设计不当导致冷却水无法使用。这时,模具表面过热只有通过大量的脱模剂喷涂来冷却模具。如果不大量喷涂脱模剂,出现粘模现象,铸件产品有顶出问题。但是大量喷涂脱模剂的结果是:模具早期出现龟裂纹并且模具的整体寿命无法达到预期的结果。
6. 热结点的温度场考量
对于大型模具,如:发动机缸体模具,由于产品有些局部壁厚比较厚,模具会有“热结点”。这时,最好的方法是考虑采用模具内部的高压点冷却(Jet cooling),其特点是高压的循环水(10-16bar)高速通过点冷水道把局部高热量带走。其后,高压气体把冷却水道的水吹干。
高压点冷的好处是:铝合金产品在点冷处迅速凝固形成致密的凝固组织其范围可达20毫米。在其后的吹气过程中,随着铝合金的凝固与散热,点冷的pin(型心)不会被产品冷却收缩而“固住”。型心不会因为“卡死”而断裂。而型心周围的致密凝固组织因为无缩孔等缺陷,为其后铝合金部件产品的加工提供保障。
7. 结语
本文讨论了模具温度场的设计概念。 在模具设计的初期就需要根据班产量考虑冷却水的安置。通过计算决定冷却水道的长度,分布,水流速度,带走的热功率等。这样,才能保障模具的表面温度均匀尽量减少脱模剂的喷涂延长模具的使用寿命。
例举的实际案例表明:如果内冷却水安装的不够,那么模具表面在生产过程中温度升高。长时间的使用模具会使得模具表面硬度下降,模具寿命缩短。另外一种情况则是:冷却水设计不当影响生产只能关闭。这样,模具的表面过热会出现粘模现象铸件产品难以顶出。此时,采用大量的喷涂脱模剂那么模具表面承受激冷急热,模具短期生产后表面出现早期龟裂纹。模具的整体使用寿命也会下降。