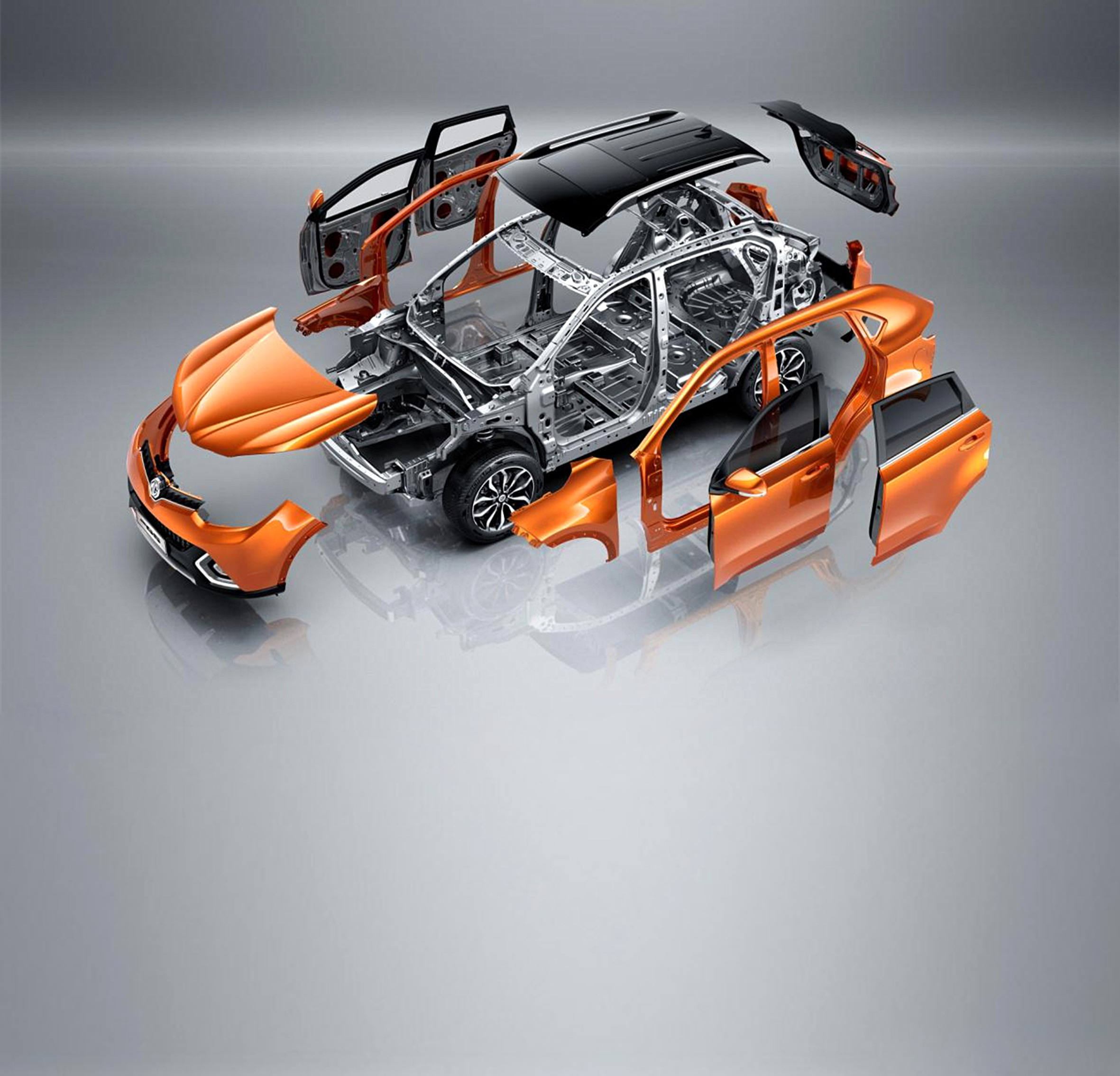
文:杨 婻
上海泛亚汽车技术中心有限公司
摘要 介绍了铝合金材料的特点和在汽车车身结构上的应用现状,并通过对铝合金材料的分类及其力学性能的研究,探讨了铝合金材料在车身结构应用上的优势和难点,展望了铝合金材料在车身结构应用上的前景。
关键词 铝合金 车身 应用
0 引言
随着世界石油储备的日益减少,车身轻量化已成为汽车制造技术发展的必然趋势,降低汽车重量最直接的方法就是在车身结构上大量使用铝合金与高强钢轻量化材料。本文主要研究了铝合金材料在车身结构上的应用。
1 铝合金的特点和应用现状
铝的密度小,仅为2.7 g/cm3(属轻金属),约为钢的1/3。由于铝的熔点较低,流动性好,易于制造各种形状复杂的零件。另外铝的表面容易氧化形成致密而稳定的氧化膜,所以耐腐蚀性也比较好。在铝中加入一种或几种元素后即构成铝合金,铝合金相对于纯铝,可以提高强度和硬度,有些铝合金还可以热处理强化,使抗拉强度超过 600 MPa。
因此它在汽车上的用量呈现持续增长的趋势,北美、欧洲和日本汽车的单车平均用铝量逐年都在增加。国外研究公司 Ducker Worldwide 调查结果显示,以铝代替钢制造汽车可使车身结构重量减轻 30% ~40%。宝马5系列采用了全铝合金的前舱结构,由铝挤压件、铸铝件、铝冲压件组成,仅重47. 6 kg,见图 1。相对于同结构的钢制前舱,节省了 30%的重量。同时这个创新结构满足了刚度、强度、成型性、制造工艺、耐腐蚀等方面的要求。
奥迪 A8、R8 和均采用了全铝合金车身。捷豹 、奥迪 R8 的车身结构材料分布见图 2,可见除 8%为高强钢之外,其余都是铝合金材料。全新一代路虎揽胜创造性地采用全铝承载式车身轻量化技术,较之前一代采用钢制车身结构的揽胜车身重量降低 39%。目前在欧洲和北美开发的超轻车计划中,铝合金已经占到 53%,这个比例将在未来几年有大幅度的提升。
2 铝合金的分类、应用和性能
车身结构所用铝合金按工艺分主要有铸造铝、挤压铝、冲压铝。铸造铝又分为重力铸造、低压铸造、高压薄壁铸造。由于车身结构一般都是薄壁零件,所以适合用高压薄壁铸造。
2. 1 高压薄壁铸铝
在高压作用下,将熔融金属高速射入压铸模具型腔,并使之在高压下凝固的一种成型方式。高压铸铝件通常被制造成能够承载大载荷的车身结构件,明显减轻重量的同时还具有较高的强度,这种工艺流动性好,这类零件具有复杂的几何形状,通常是采用真空压铸的方式,使它们具有高强度的同时还具有很好的延展性、良好的焊接性能和较高的可塑性,保证它们在碰撞时有很好的安全性。如图 2 所示,奥迪 R8 的前纵梁后段、后纵梁前段、前后轮罩等主要结构件用的都是高压薄壁铸铝件。
高压薄壁铸铝零件的特性主要取决于铝合金材料的化学成分,表 1 列举了常用铸造铝合金的力学性能。车身结构件所用的高压薄壁铸铝零件在达到较高抗拉强度和屈服极限的同时还必须具备超高的韧性,延伸率一般要求大于 10%。
2. 2 挤压铝
铝挤压型材经过液压校正或者 3D 弯曲加工,制造出具有一定力学性能的车身零件。近年来,随着挤压铝加工技术的发展,型材的高精度 3D 弯曲加工技术以及 6 千系列铝合金材料的组织控制和均一屈服强度控制热处理技术的确立,使铝挤压在汽车上的应用空间得到极大的扩展。一般适用于等截面的结构件,例如前纵梁前段、门槛、后纵梁后段。图 3 是奥迪 A2 的车身结构框架示意图,大大增加了挤压铝的用量。
车身用挤压铝零件的材料大多是 6000 系列和 7000 系列,同时为了加强缓冲,提高抗冲击强度,型材断面多采用“口”、“日”、“目”字形。7000系列合金强度比 6000 系列合金高。车身用挤压铝型材的力学性能见表 2。
2. 3 冲压铝
冲压铝在车身上的应用已经比较成熟,多用于外覆盖件和一些强度要求不高的薄壁零件,例如侧围外板、顶盖、地板等。车身所用铝板主要有5000 系列(Al-Mg)和 6000 系列(Al-Mg-Si)。车身常用铝板的力学性能见表 3,铝合金板的延伸率和 r 值远远小于钢板,所以当铝合金板代替钢板时,可能出现局部拉延不好,容易产生裂纹。在结构设计时要尽可能地保证形状不突变,让材料容易流动以避免开裂。
3 铝合金应用的主要难点
(1) 铝合金板材的深冲压性能较差,容易产生裂纹,所以应尽量减少集中拉伸。深拉伸时要进行良好的润滑并采用异形坯料,必要时可增加工序。另外,铝合金板材的尺寸精度不容易掌握,回弹难以控制,在形状设计时要尽可能采用不易回弹的形状。
(2) 因为铝比钢软,在生产和运输中的碰撞、各种粉尘附着、空气污染等原因使零件表面产生碰伤、划伤、污渍等缺陷,从而对零件的连接造成影响。所以要对模具和设备的清洁、环境的粉尘、空气污染等方面采取措施,确保零件的清洁和完好。
(3) 铝钢的连接技术目前还不成熟。由于铝和钢的晶体结构、物理及化学性质相差悬殊,异种金属连接极易生成脆性金属间化合物 (FeAl、FeAl3、Fe2Al5),而且铝合金表面的氧化膜的存在都对接头性能有很大影响。目前采用的机械连接方法(如铆接、自攻螺钉)有如下缺点:连接的气密性较差、会留下明显的连接痕迹、对车身零件的公差要求高等。随着铝合金材料在车身结构上应用的广泛,各主机厂对铝钢的机械连接正在做一系列的深入研究:连接型面之间涂胶、机械连接位置的选择尽量避免外露、提高车身零件的尺寸稳定性等。同时建立连接技术的数据库,使连接的强度和可靠性、效率、质量控制得到理论分析的支持,最终能更有效地应用在铝制车身上。
4 结语
汽车工业中,零件的轻量化和高强度对于汽车的节能降耗、提高安全系数有显著作用。铝合金因为具有良好的成型性能和较好的强度、耐腐蚀性且成本低等优点,被越来越多地应用到车身中。提高汽车用铝量,实现车身轻量化,已经成为当今汽车制造业技术进步的一个重要环节。虽然铝合金还存在一些缺点,但随着技术和工艺的发展,这些问题也会迎刃而解。预计在不久的将来,国内外汽车对汽车用铝的需求量会大大增加。